Digital Twin d’une nouvelle ligne de production
Nombre d’heures projet : 750 heures
Durée du projet : 6 mois
Nombre de techniciens : 3
Attente client
Un verrier français a récemment investi dans l’évolution d’une de ses usines d’Europe de l’Est spécialisée dans la fabrication de verre pour les marchés du bâtiment et de l’éco-construction. Avec cet investissement, le verrier souhaite repenser sa ligne de fabrication de plateaux de verre à haute technicité en ajoutant un ilot de traitement. Objectif : L’amélioration de la qualité de ses produits.
Solution DV GROUP
Pleinement impliqué dans l’industrie 4.0 et le développement des usines intelligentes, le verrier souhaite utiliser la technologie Digital Twin.
Les objectifs sont clairs :
- Virtualiser la machine pour sécuriser les différentes modifications mécaniques et d’automation
- Vérifier la gestion des nouveaux flux de production
- Réduire les temps d’immobilisation de la ligne
Avec ces objectifs précis, notre client nous confie la modélisation de cette nouvelle ligne.
Travaux réalisés
Solution technique DV GROUP
Phase 1 : Analyse et relevés sur site
L’objectif de cette première phase est de vérifier l’aspect dimensionnel de la ligne dans le but d’alimenter le système et ainsi obtenir un modèle 3D fidèle à la réalité. Pour cela, nos experts ont effectué une campagne de mesures afin de relever l’ensemble des caractéristiques dynamiques de chaque équipement comme les vitesses ou encore les accélérations/décélérations.
Phase 2 : Modélisation de l’existant
Sur la base du plan d’implantation 2D et des relevés sur site, nos experts ont modélisé puis animé la ligne existante en 3D sur le logiciel SIEMENS NX MCD. En effet, l’ensemble des mouvements (capteurs et actionneurs) sont connectés au programme via des tables d’échange « temps réel » permettant ainsi le pilotage de l’environnement 3D par le programme automate. Puis le modèle a été testé lors d’un « virtual commissioning » (mise en service virtuelle) de la ligne. L’objectif étant de vérifier que le « Digital Twin » soit parfaitement identique à la ligne existante. Ainsi, l’ensemble des cycles automatiques, les temps de cycles et le comportement du verre ont été testés.
Phase 3 : Modélisation des nouveaux équipements
Sur la base de notre modèle initial, nos experts ont modifié l’installation et implanté les nouveaux équipements dans le modèle 3D. Puis le nouveau programme automate a été développé. Afin de valider l’ensemble, un deuxième « virtual commissioning » en condition réelle de production a été effectué. Cela a notamment permis de visualiser l’ensemble de la ligne, tester tous les cas de figure, les cycles de production ainsi que ses aléas.
Phase 4 : Mise en service sur site
La dernière phase du projet a été consacrée aux tests électriques, modes manuels et essais (à vide et en charge). Comme l’ensemble de la ligne et des cycles de production ont été testés sur le Digital Twin lors de la phase précédente, seul 50 plateaux de verre ont suffi lors des essais en charge avant la mise en production en pleine cadence.
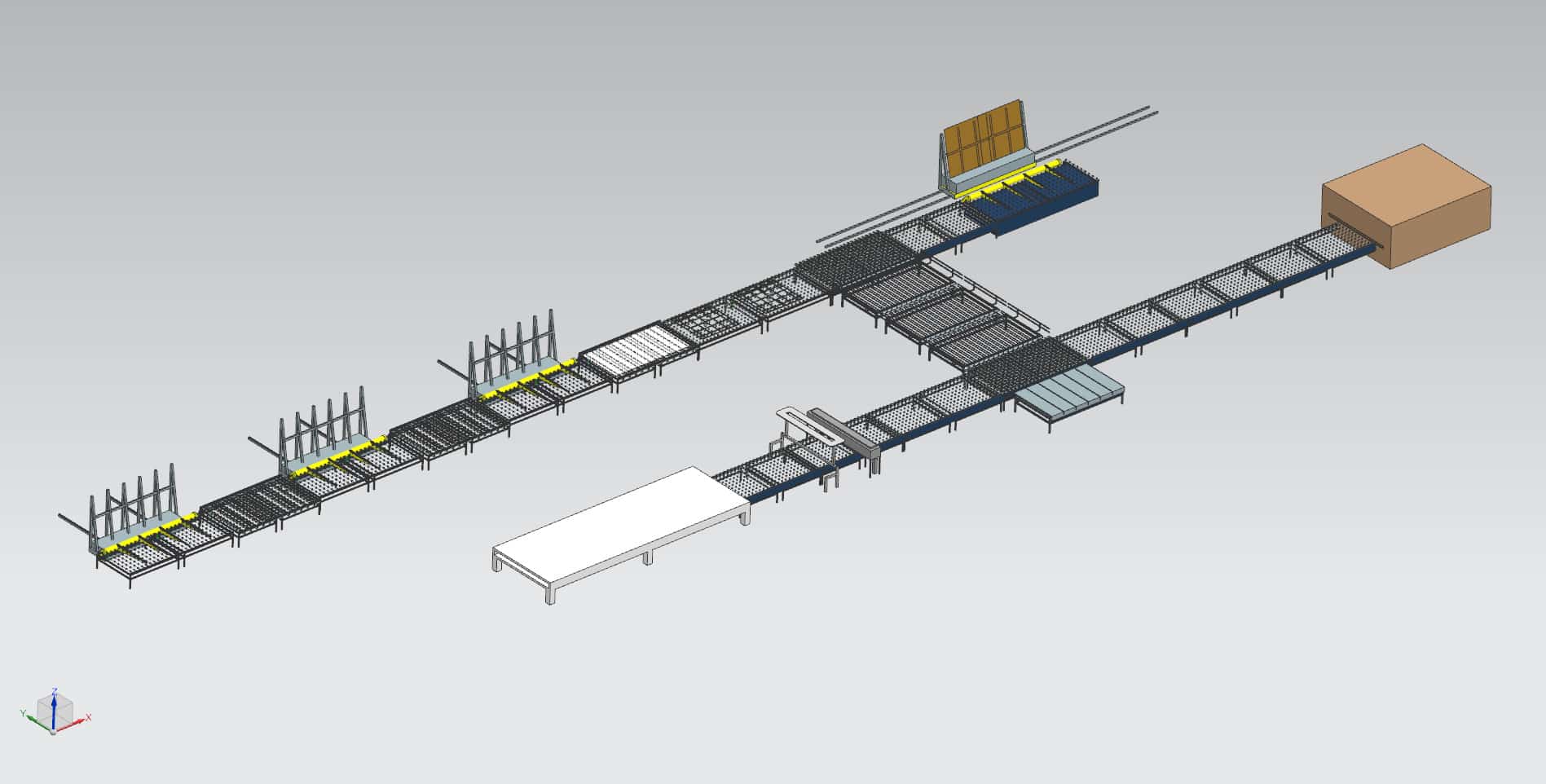
Gains et bénéfices client
- Qualité : Optimisation des fonctionnalités de la ligne dans son environnement virtuel et amélioration de la qualité programme
- Rapidité : Gain de temps de plus de 50% sur la mise en service réelle
- Efficacité : Optimisation de la programmation, des essais de mise au point et de mise en service donc réduction des heures d’ingénierie sur site
- Sécurisation : Réduction des risques et minimisation des arrêts de production
- Formation : Formation des opérateurs aux nouvelles fonctionnalités en amont