2 LEROY SOMER 600 kW variators
Number of project hours: 140 hours
4 technicians
Client expectation
Our client, one of the world leaders in the transformation of agricultural production into foodstuff ingredients, called on our experts to intervene on two 600 kW Leroy Somer variators which had broken down. Indeed, part of its factory was at a standstill and they wished us to urgently repair them onsite as:
- It would take several weeks to supply new variators
- The handling of new variators is delicate, given that the variators are on the 1st floor at the back of an electrical room.
DV GROUP solution
He asked us to urgently intervene onsite in order to limit as far as possible stoppages, as well as losses. The urgent expertise revealed the presence of acid, which had significantly damaged the condensators of both products, as well as the entry-bridge and card of the first variator. To remedy this, our experts:
- Dismantled the arm modules and entry-bridge of variator No. 2
- Cleaned up both variators
- Put the protistors in place
- Reassembled both variators
- Proceeded with trials: variator No. 2 was restarted. On the other hand, the CPU card and supply to variator No. 1 were found to be out-of-order, leading our experts to replace them.
Following this intervention and several breakdowns encountered on the variators the previous months, we advised our client to undertake an audit of their installations, as well as an action plan. Satisfied with our recommendations and our offer, our client chose to entrust us with the carrying out of preventive measures on nine of its 250 to 900 kW variators. Our experts are currently processing the turbines, as well as the power bridges.
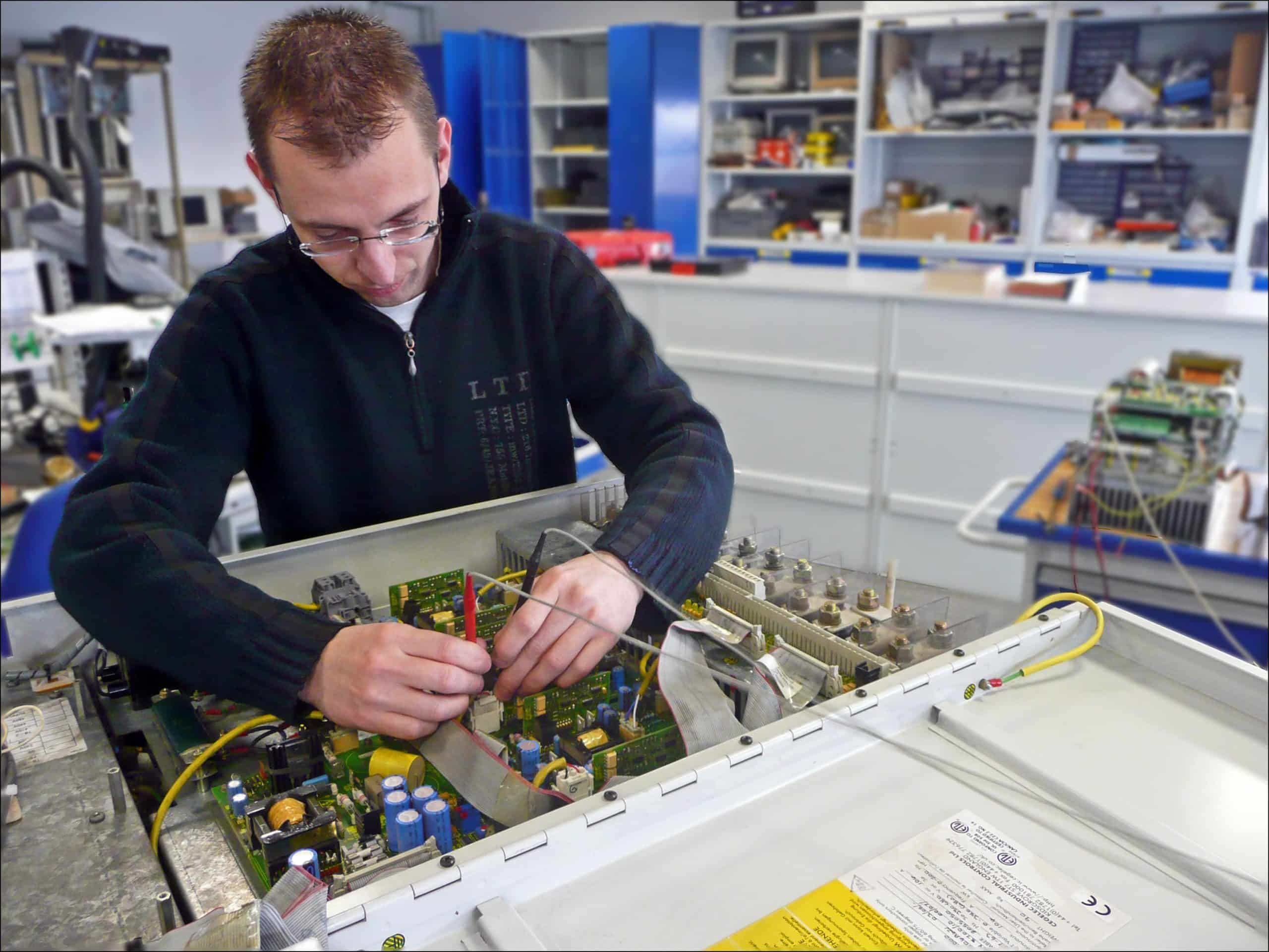
Clients gains and benefits
- Speed: variators processed in a few days, contrary to several weeks for a new solution
- Savings: low cost compared to replacing with new
- Reliability: nine variators made more reliable
- Decrease in breakdowns: decrease in uncontrolled production stoppages and therefore maintenance costs and production stoppages
- Establishment of a climate of trust: frequent, on-going exchanges and support from a dedicated DV GROUP contact
Expertise
We provide you with engineering, maintenance and control solutions based on our knowledge of your processes.
Case studies
You may also be interested in
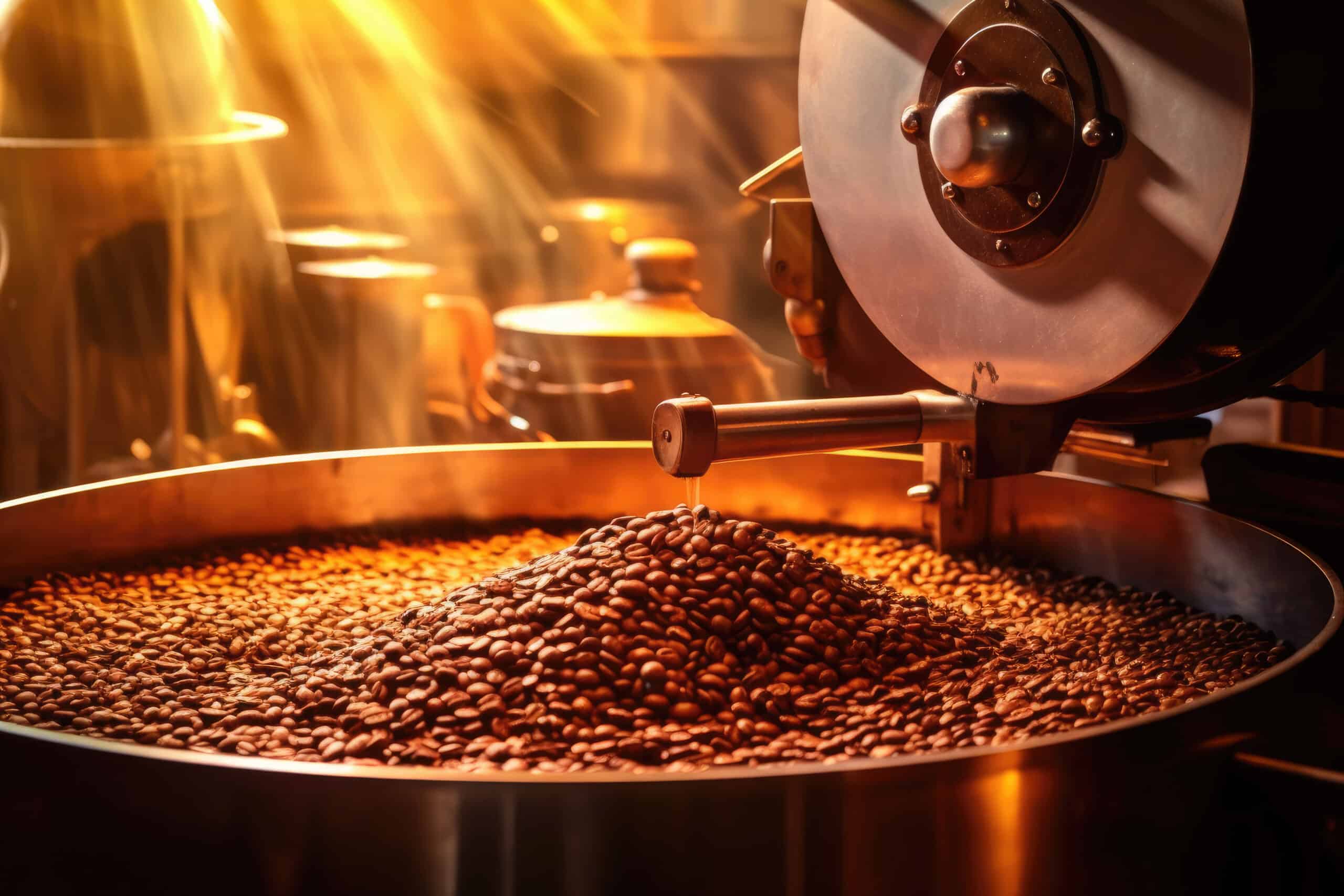
Vibration monitoring of a coffee production line
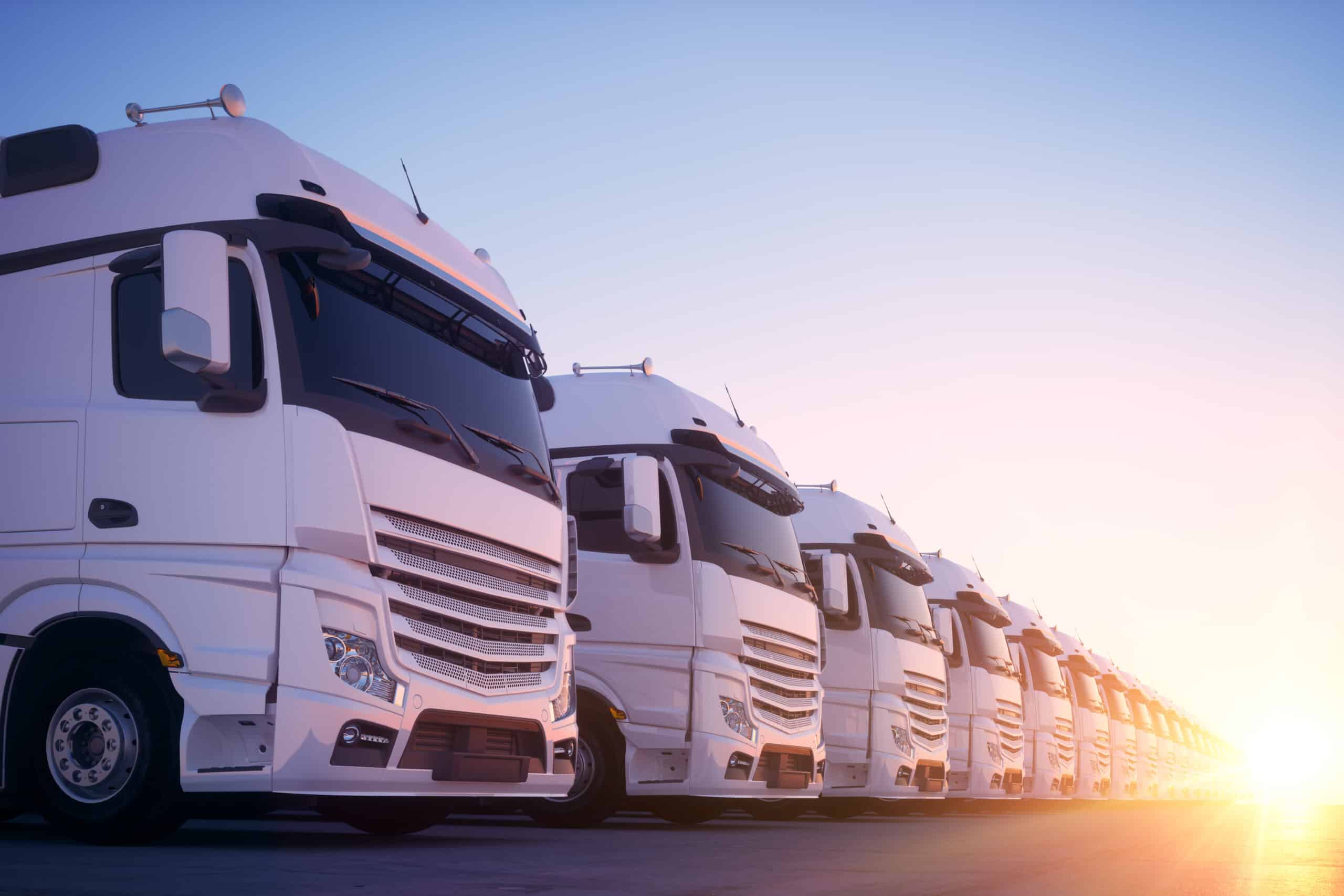
Obsolescence Management: Audit of a Truck Engine Factory’s Equipment Fleet
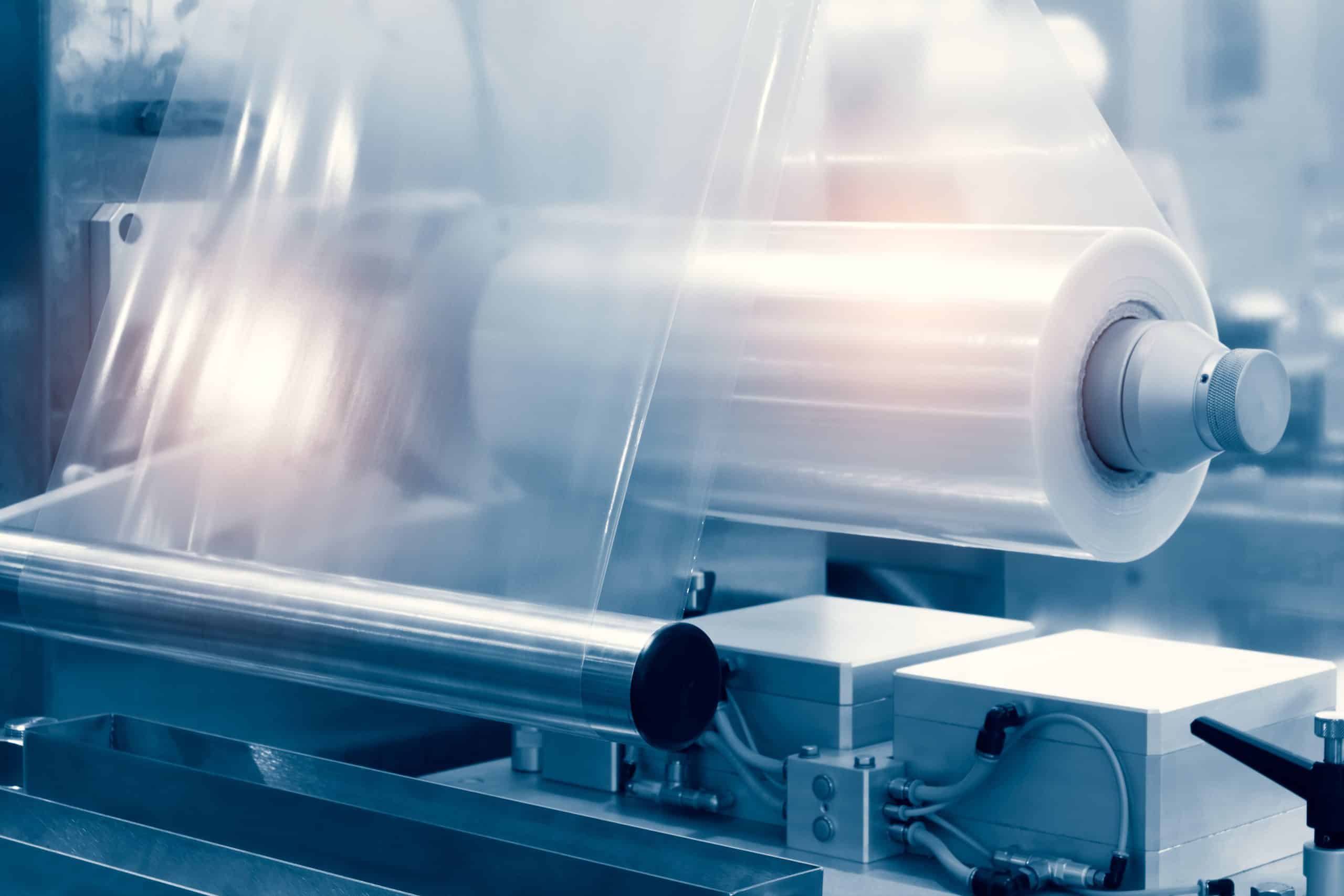
Repair and reliability of drives
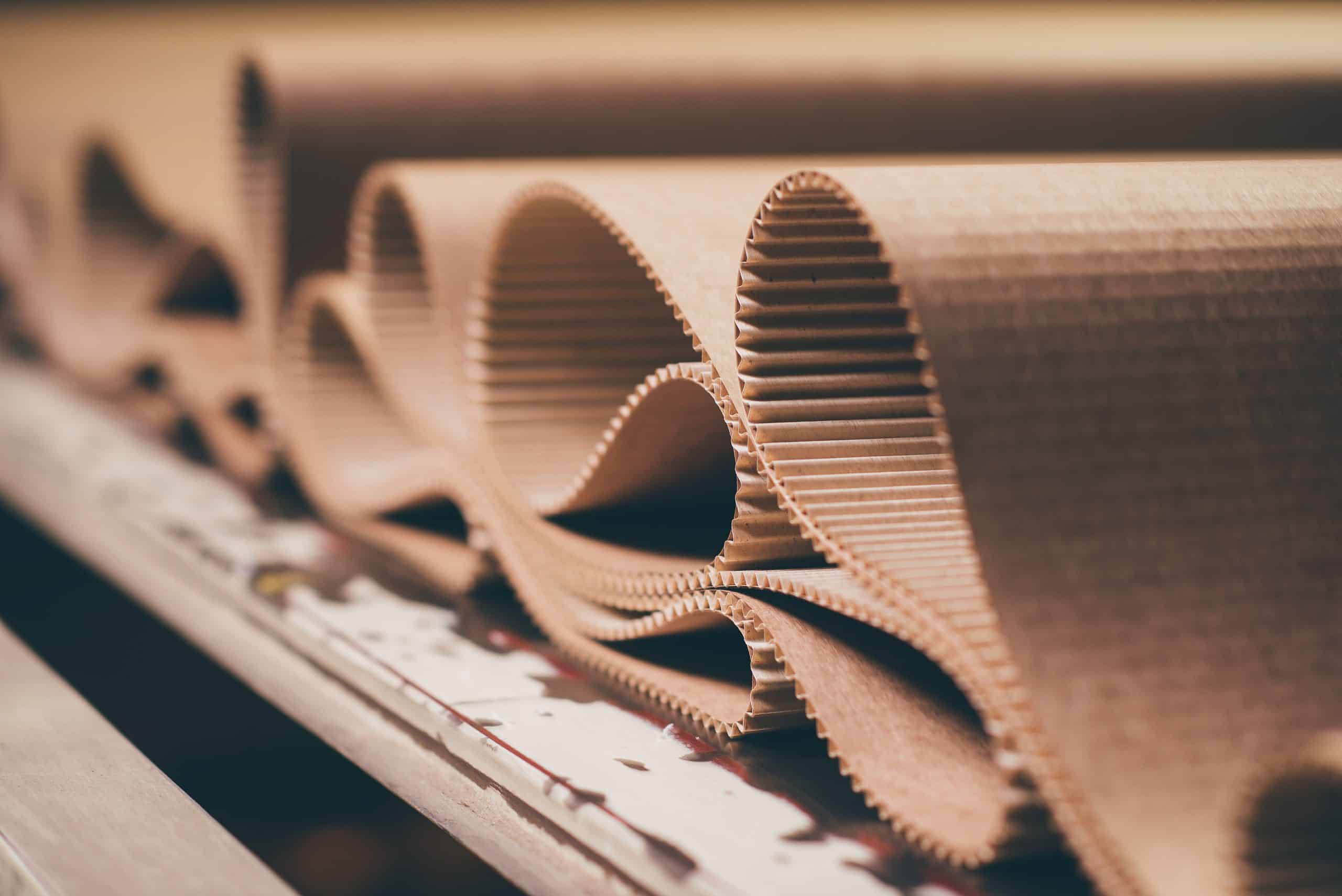
ELOPAK: Corrective preventive electronic maintenance
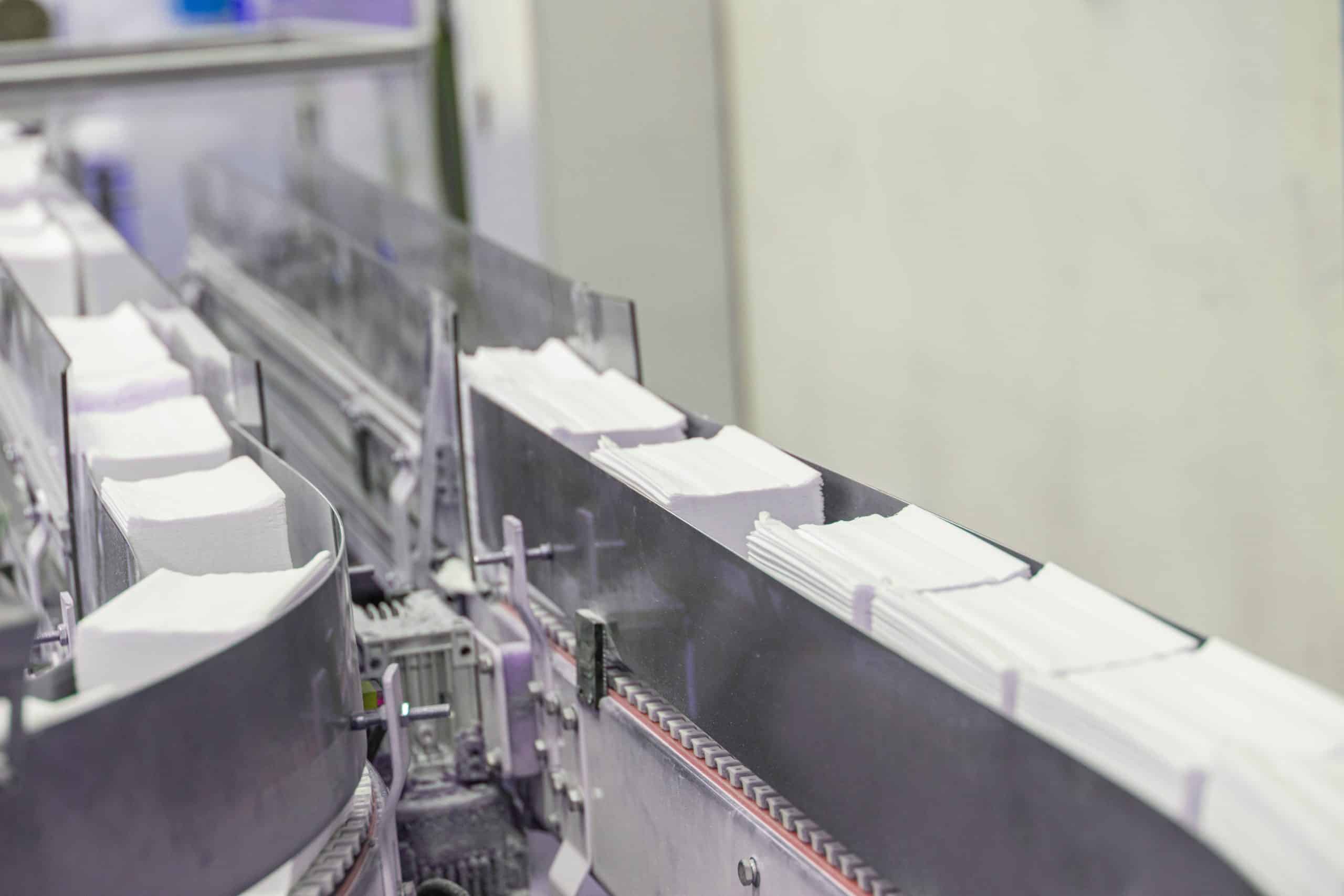
Preventive maintenance of Siemens Masterdrives
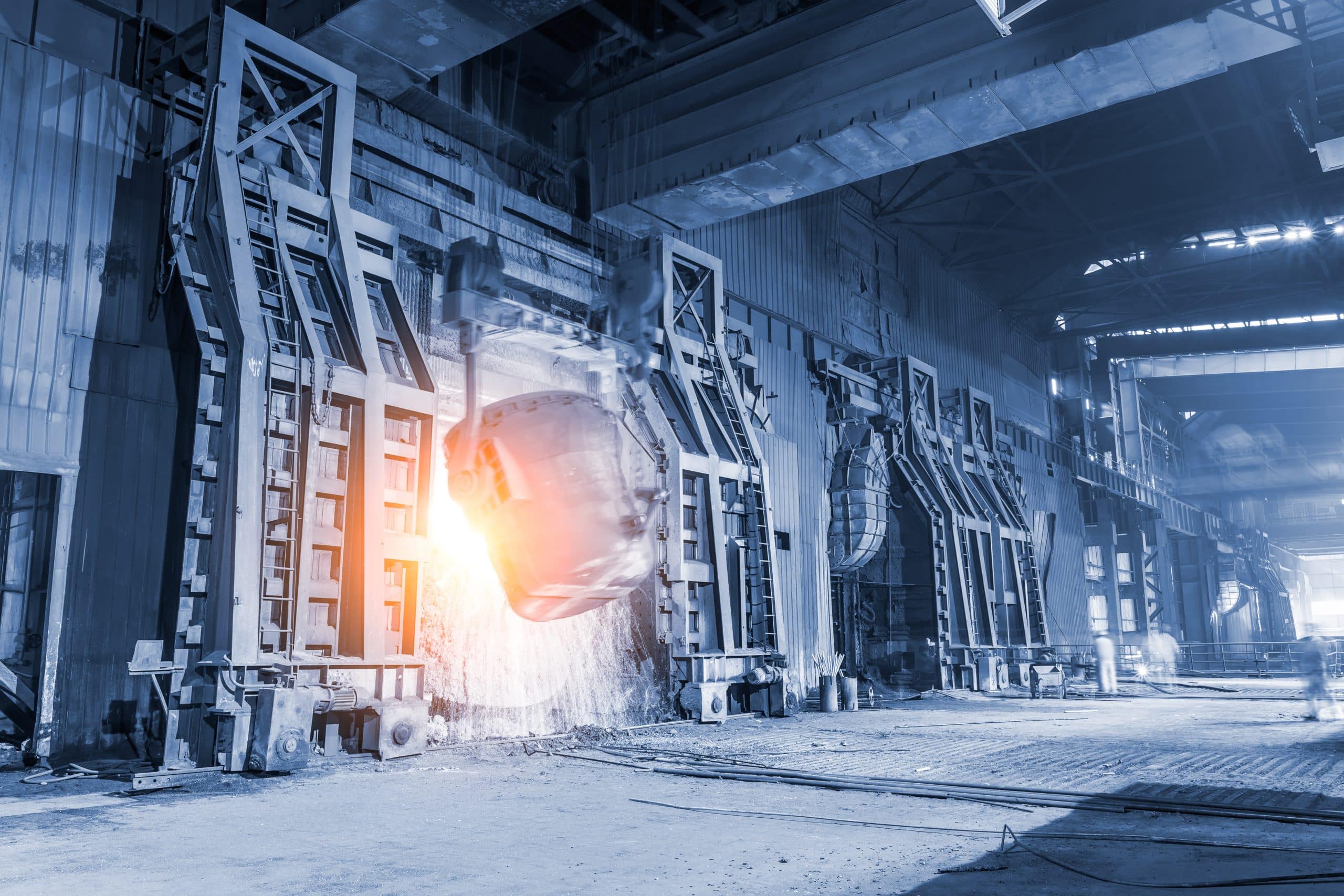
43 Simovert Masterdrive drives from 0.75 kW to 700 kW
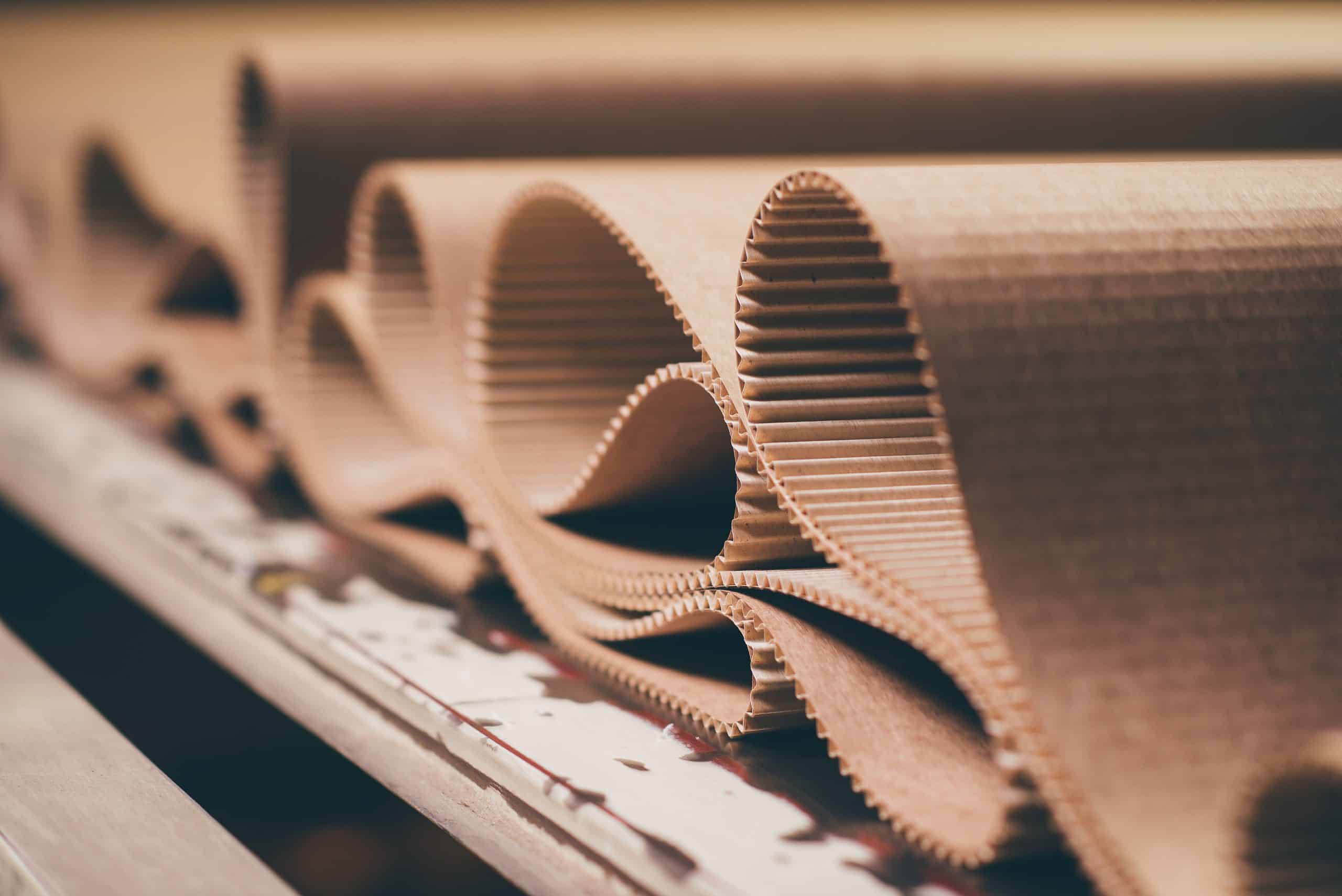
To safeguard the reliability of 32 Siemens (6SE70) Masterdrives on a paper machine section
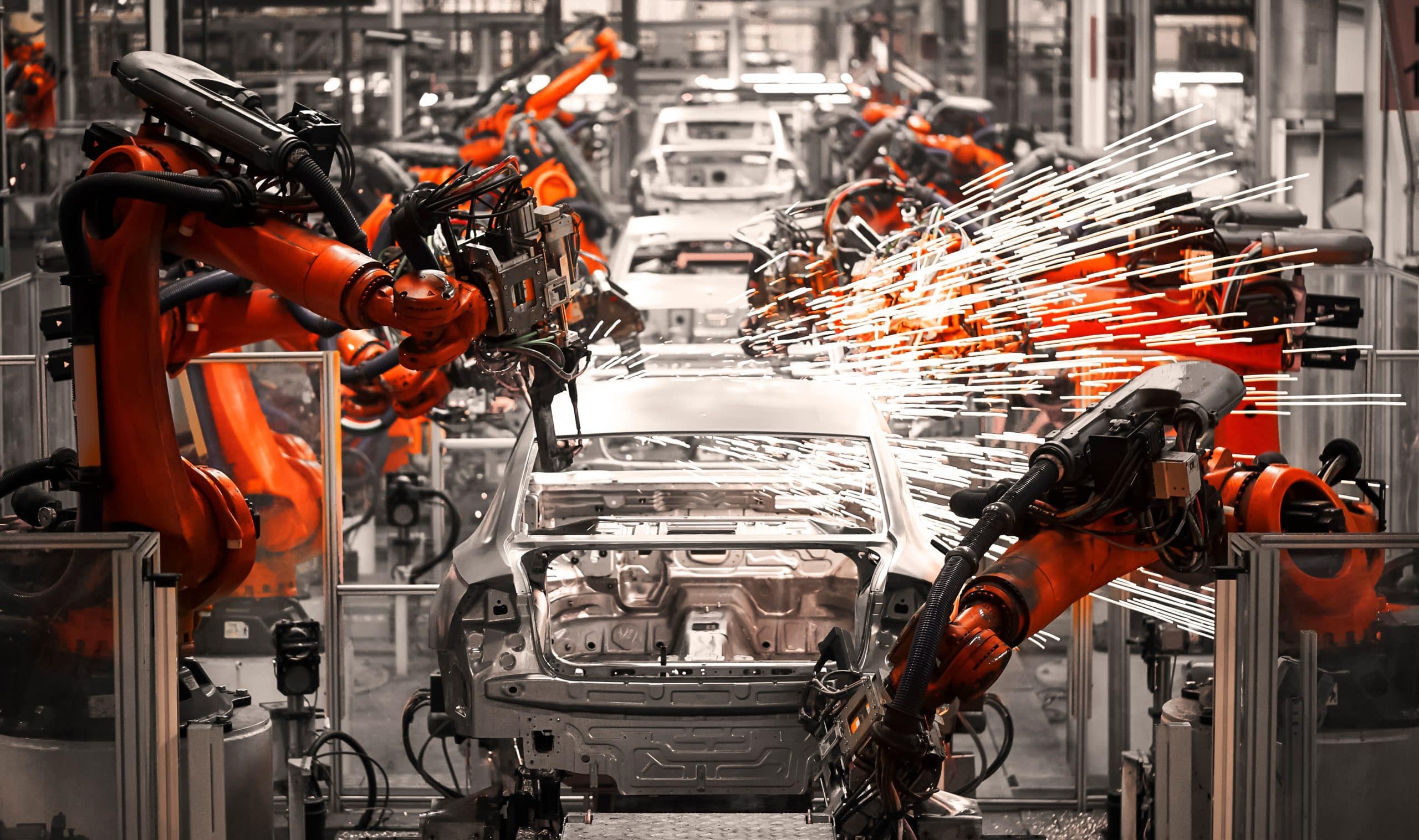
MELEGHY: Preventive maintenance of 24 Siemens Powerblocks drives
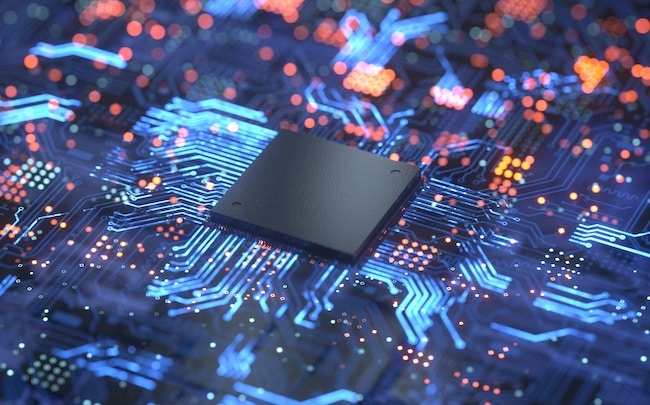
Preventive maintenance contract
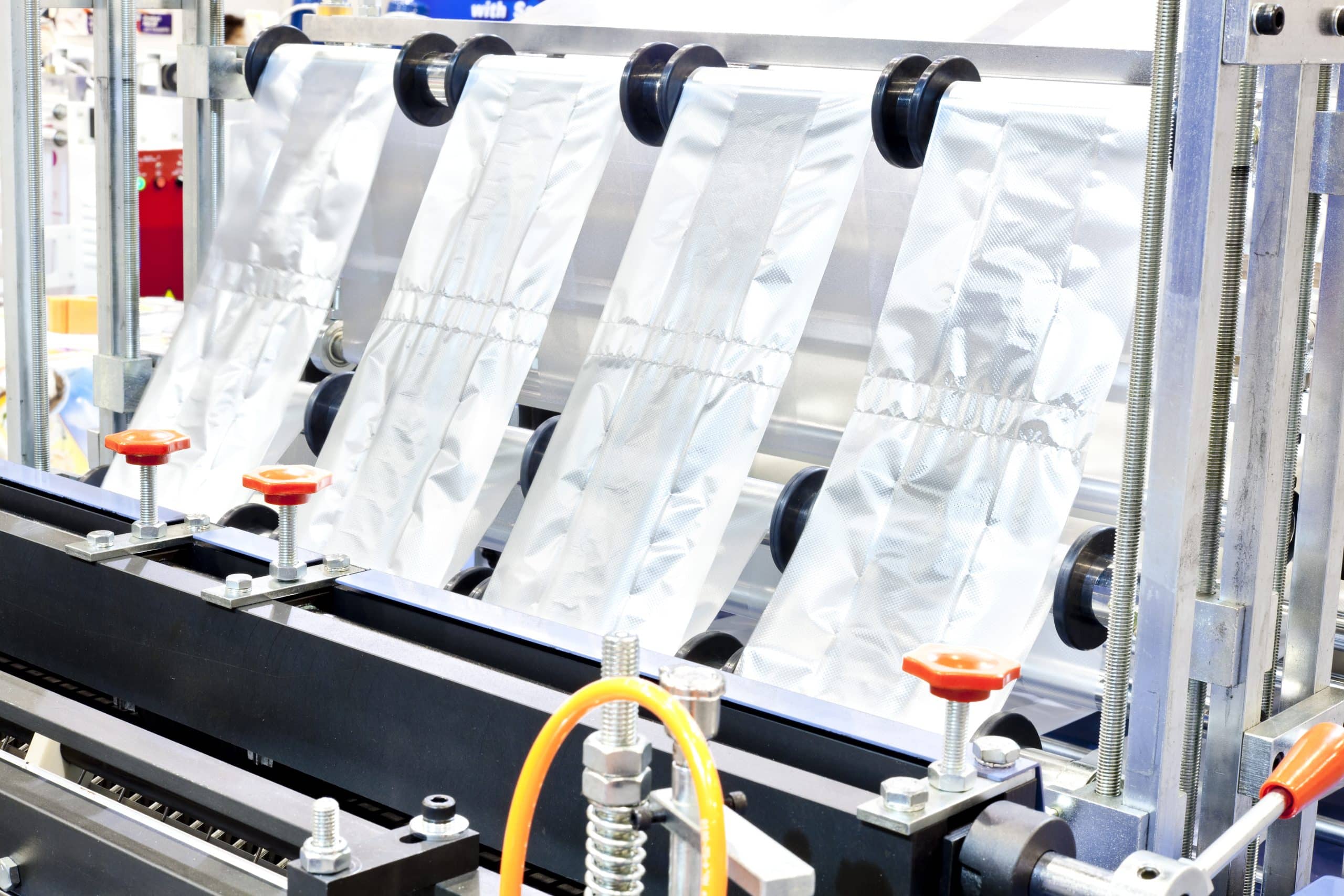
Emergency repair on a 120KW ABB ACS800 drive
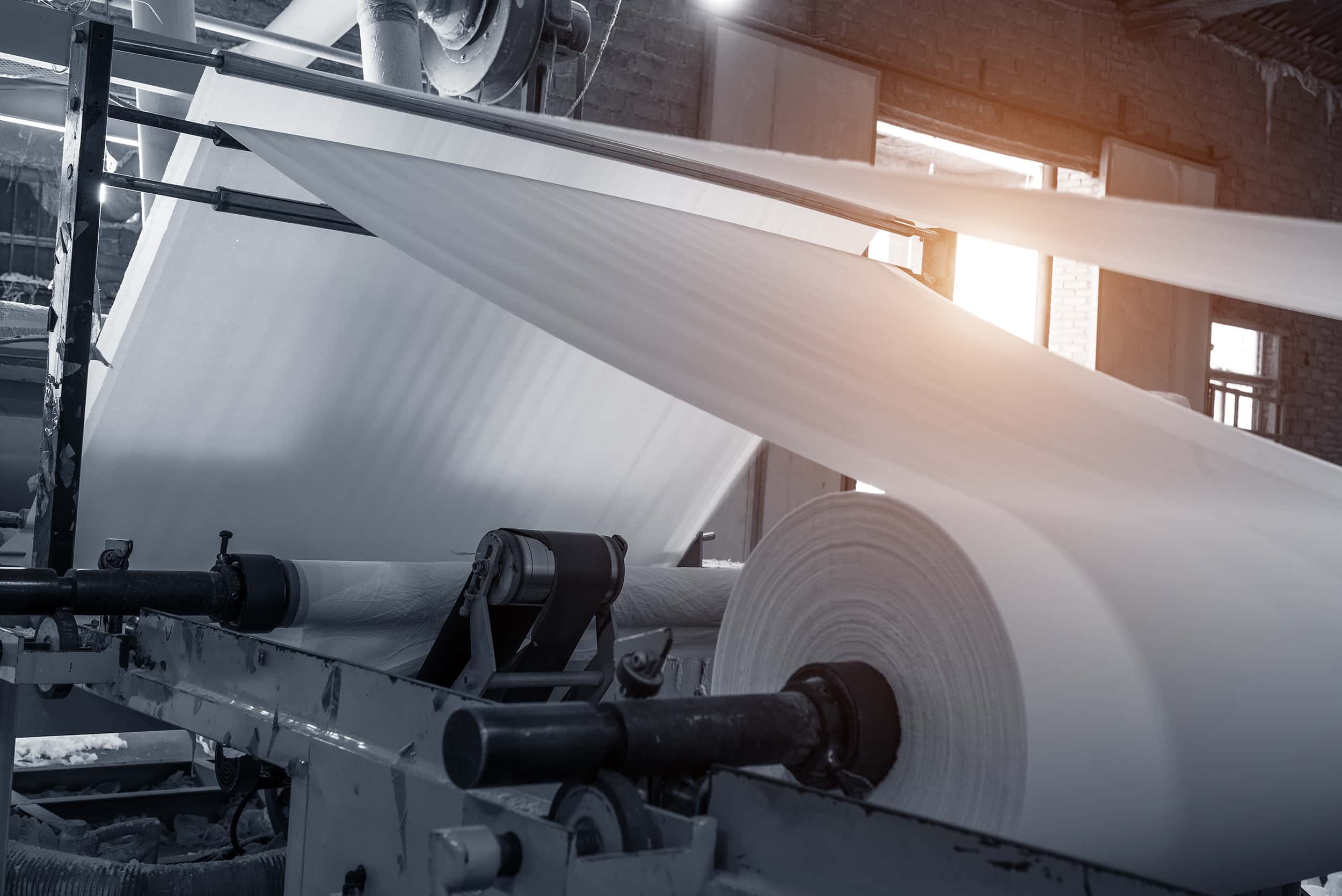
Overhaul of 12 Siemens Torque Simotics T-1FW3 motors
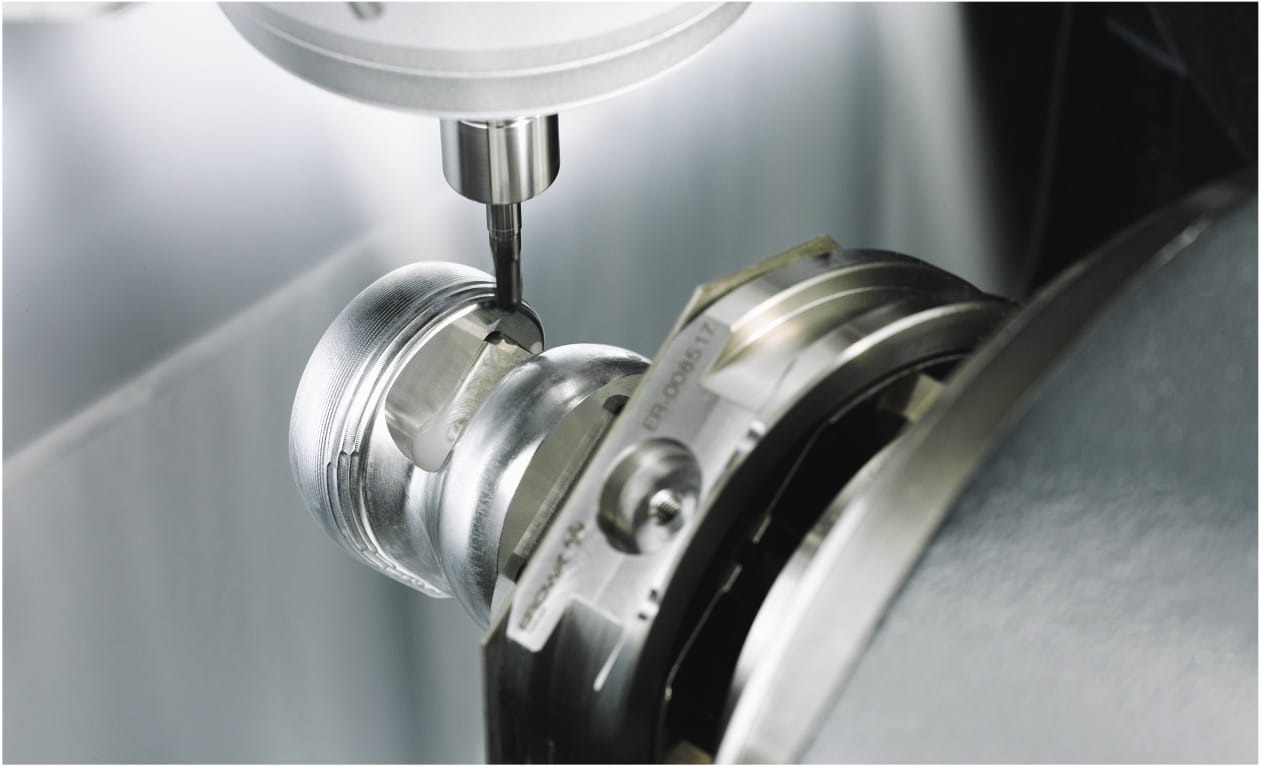
Preventive maintenance for 17 Siemens servomotors and drives
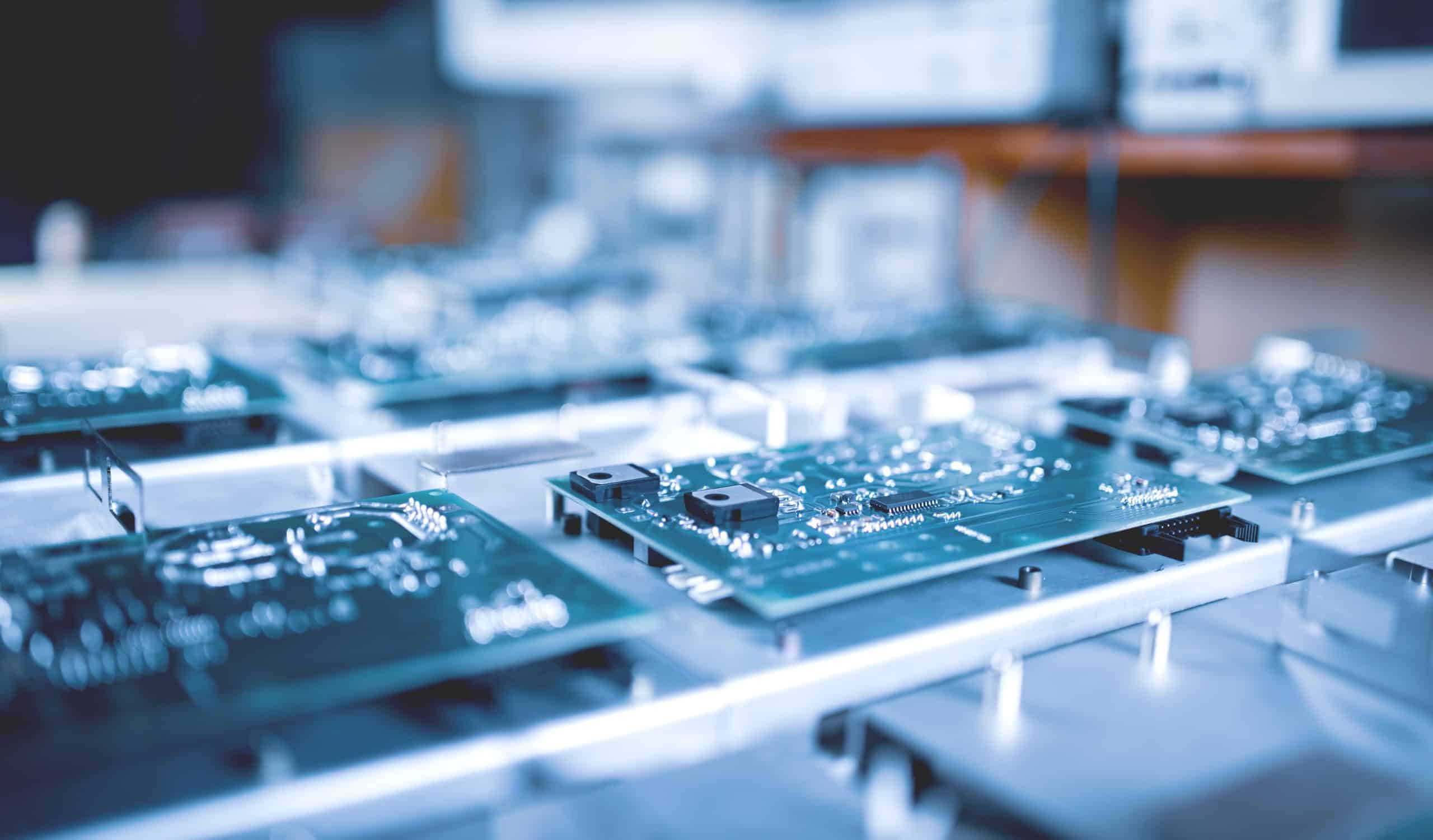
X-FAB : Replacement of two extractor fans
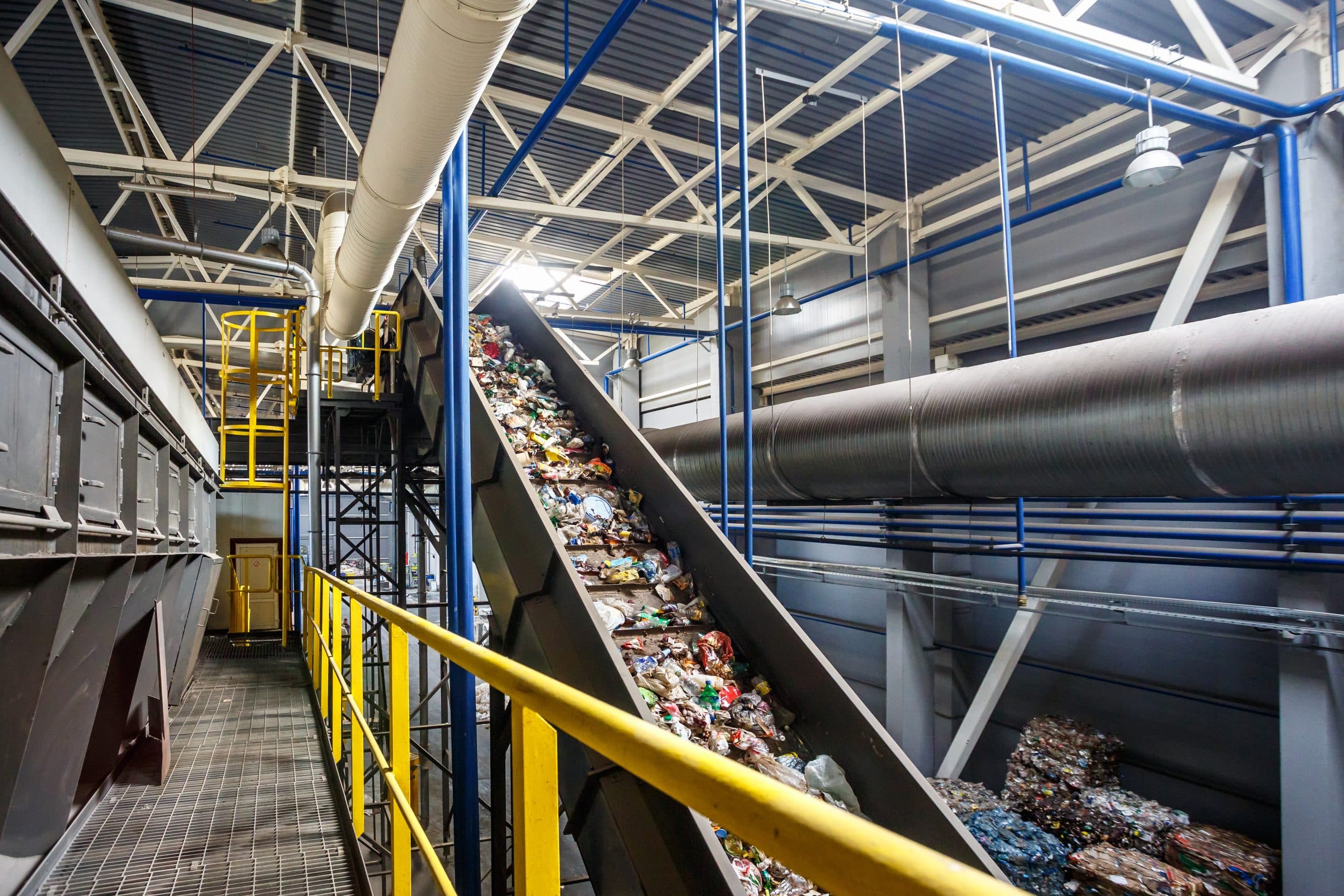
Troubleshooting of an induced draught fan
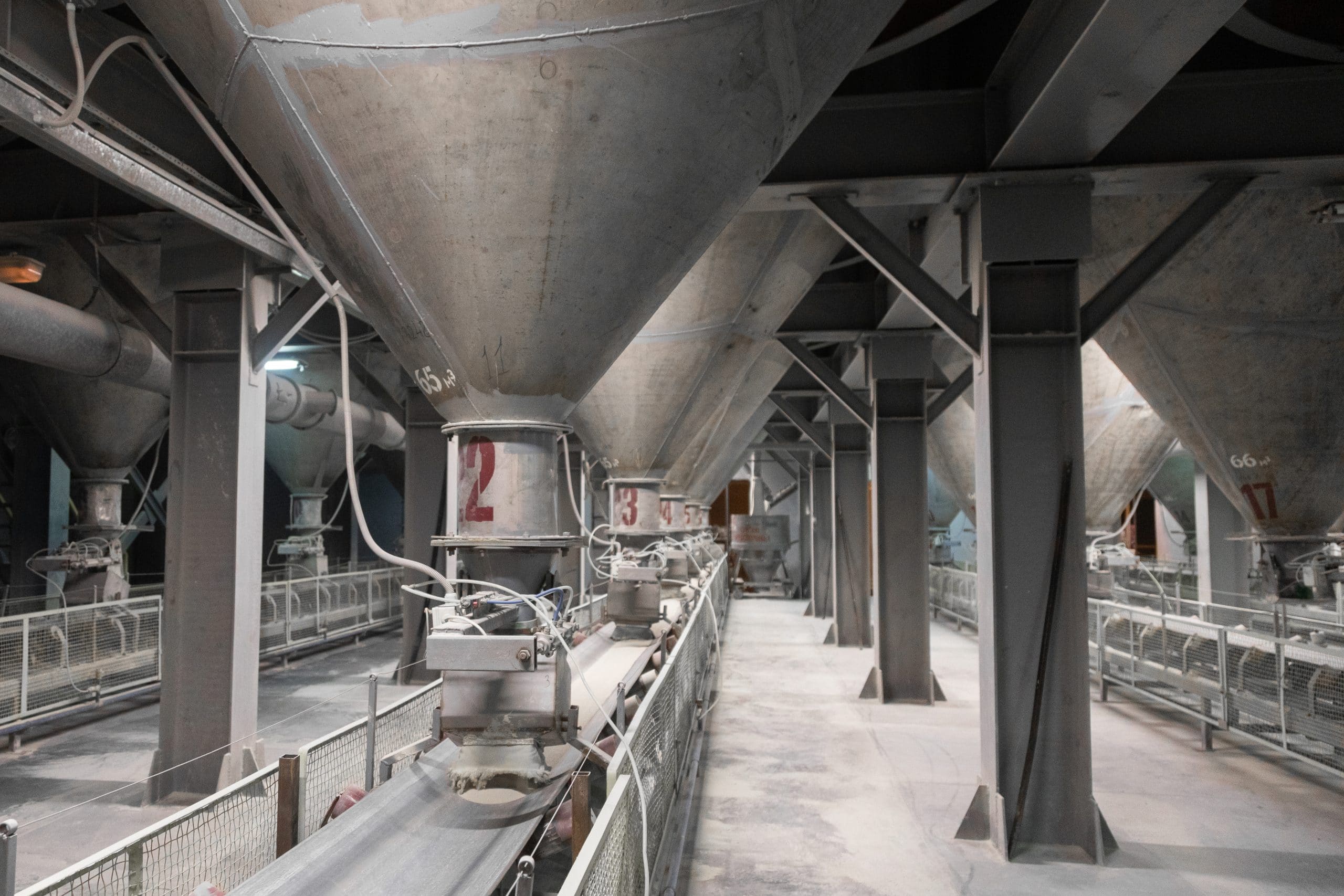
19 50 kg (2.2 kW) to 5 ton (7.2MW) motor/reducer/ventilator assemblies
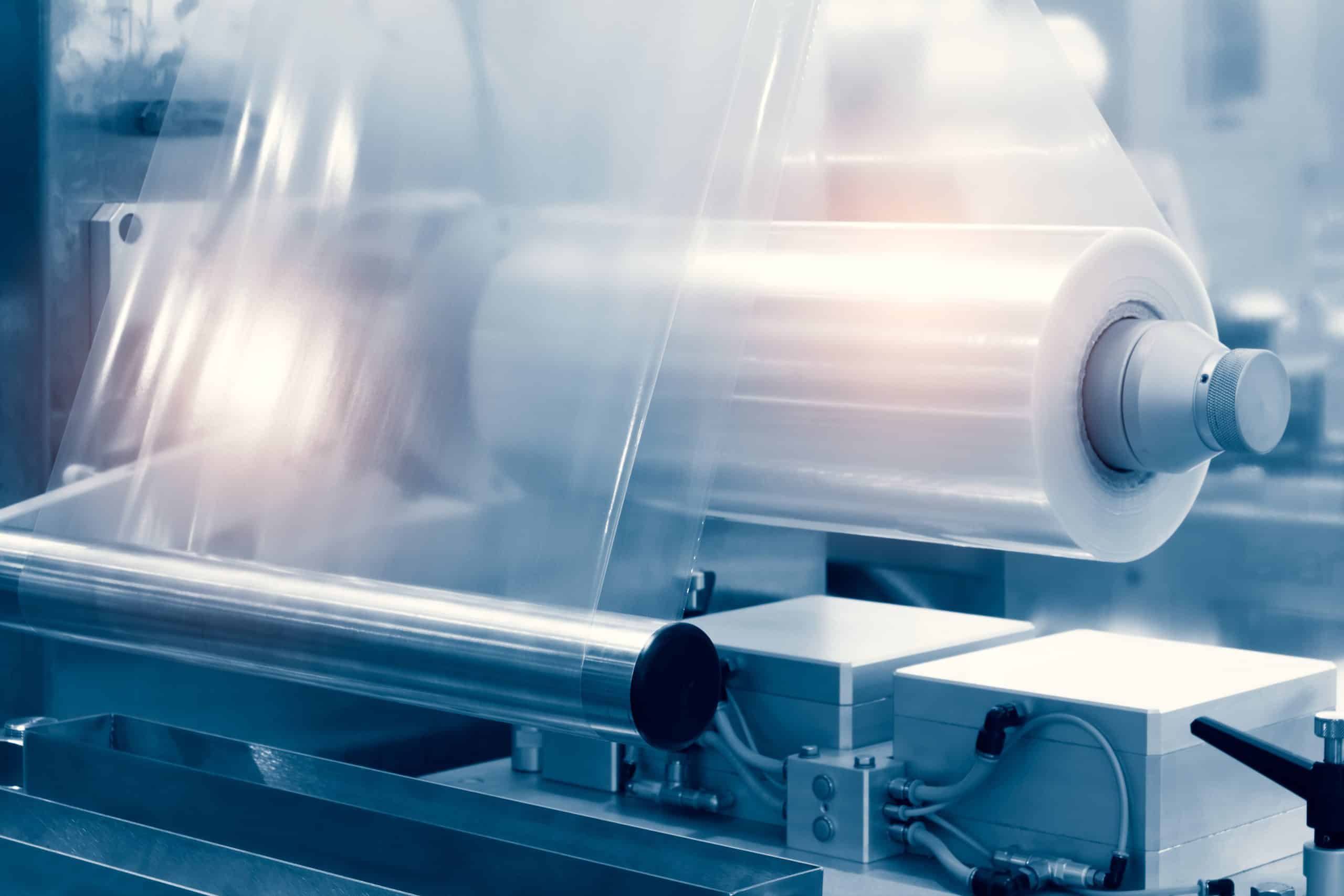
Overhaul of an extruder reducer with 2 indexed output shafts
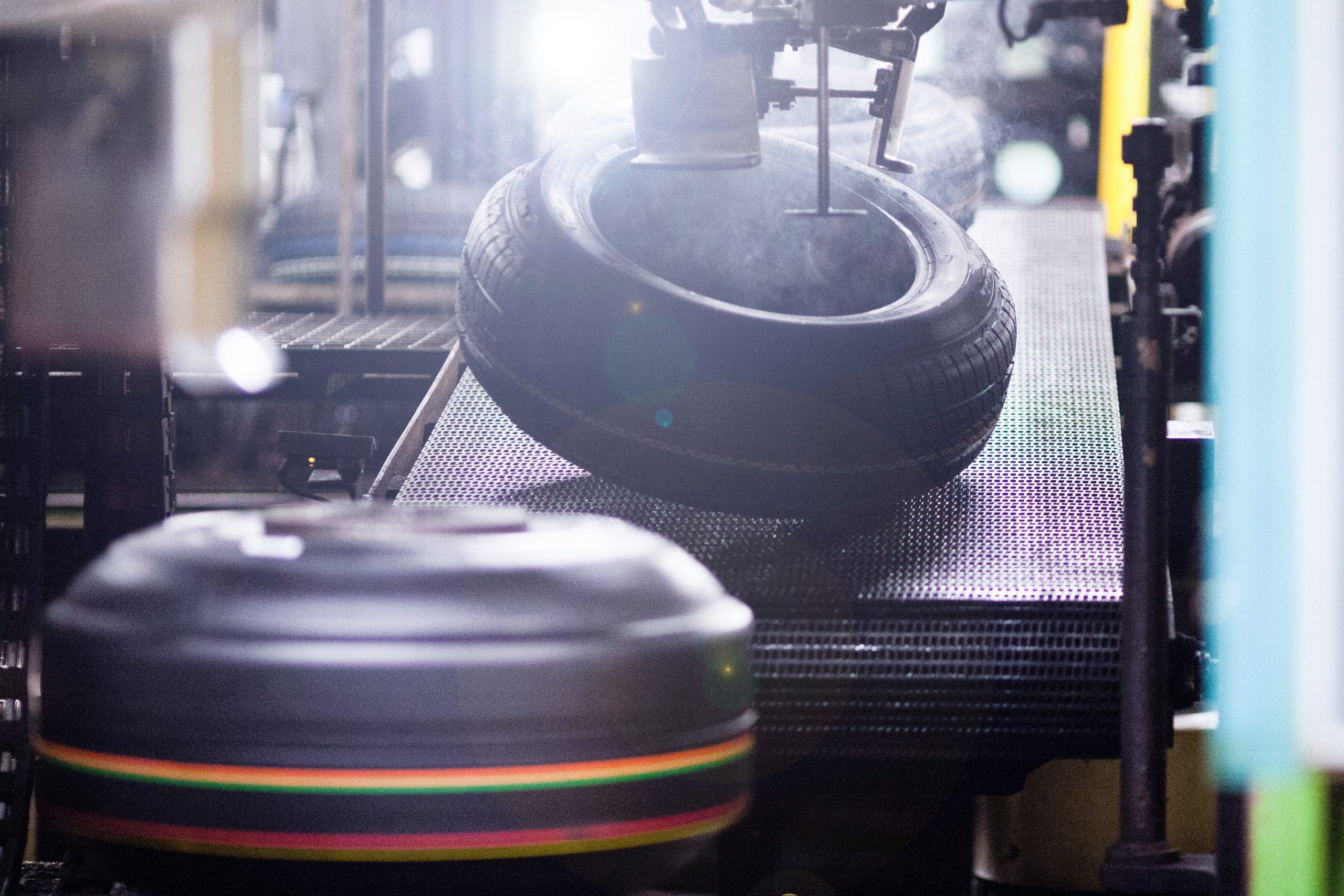
Maintenance électronique et électromécanique de 3 installations Banbury (moteurs CC et variateurs)
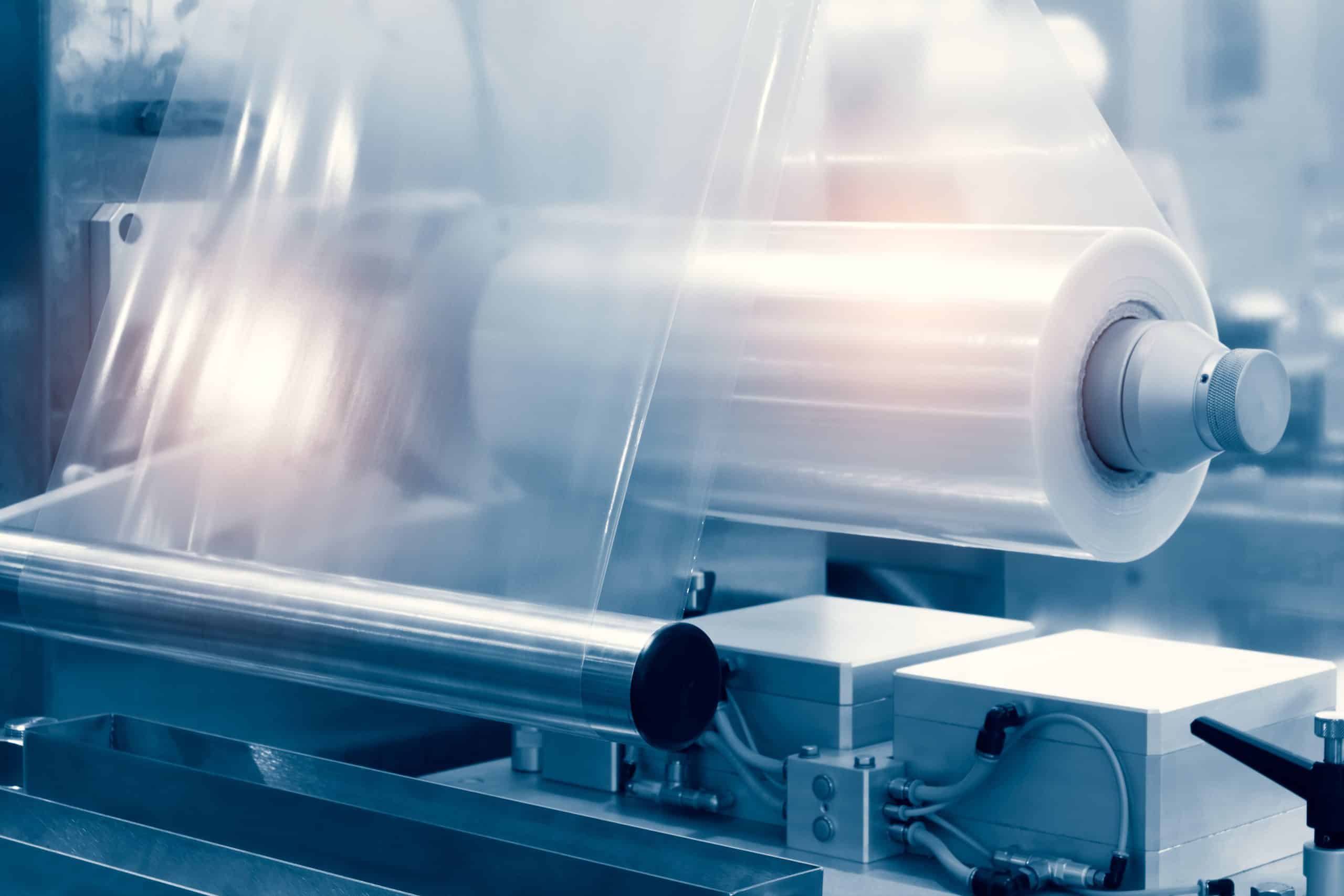
Moteur Siemens 450 KW avec mode de refroidissement à eau
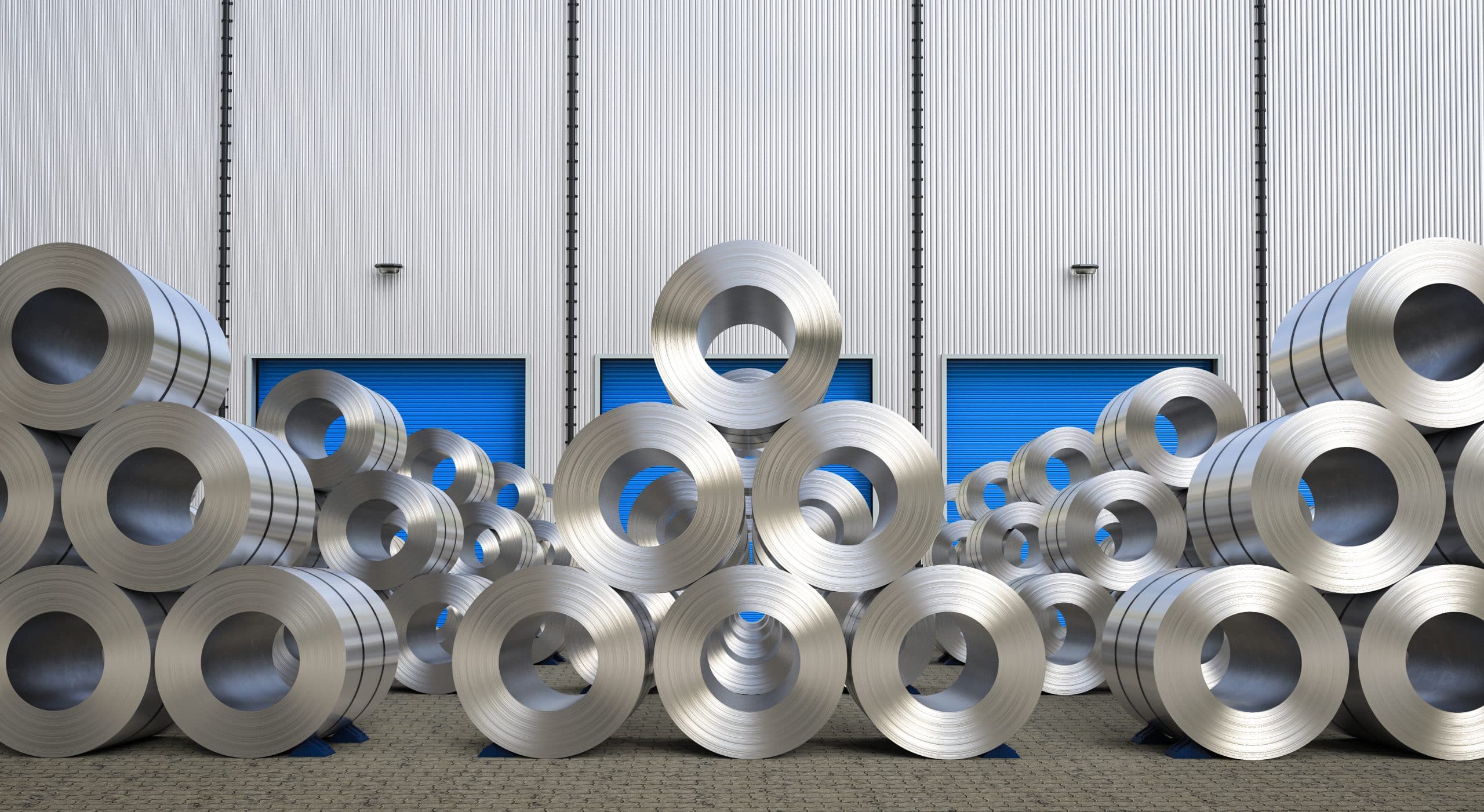
Révision d’un moteur CC 540 KW de laminoir
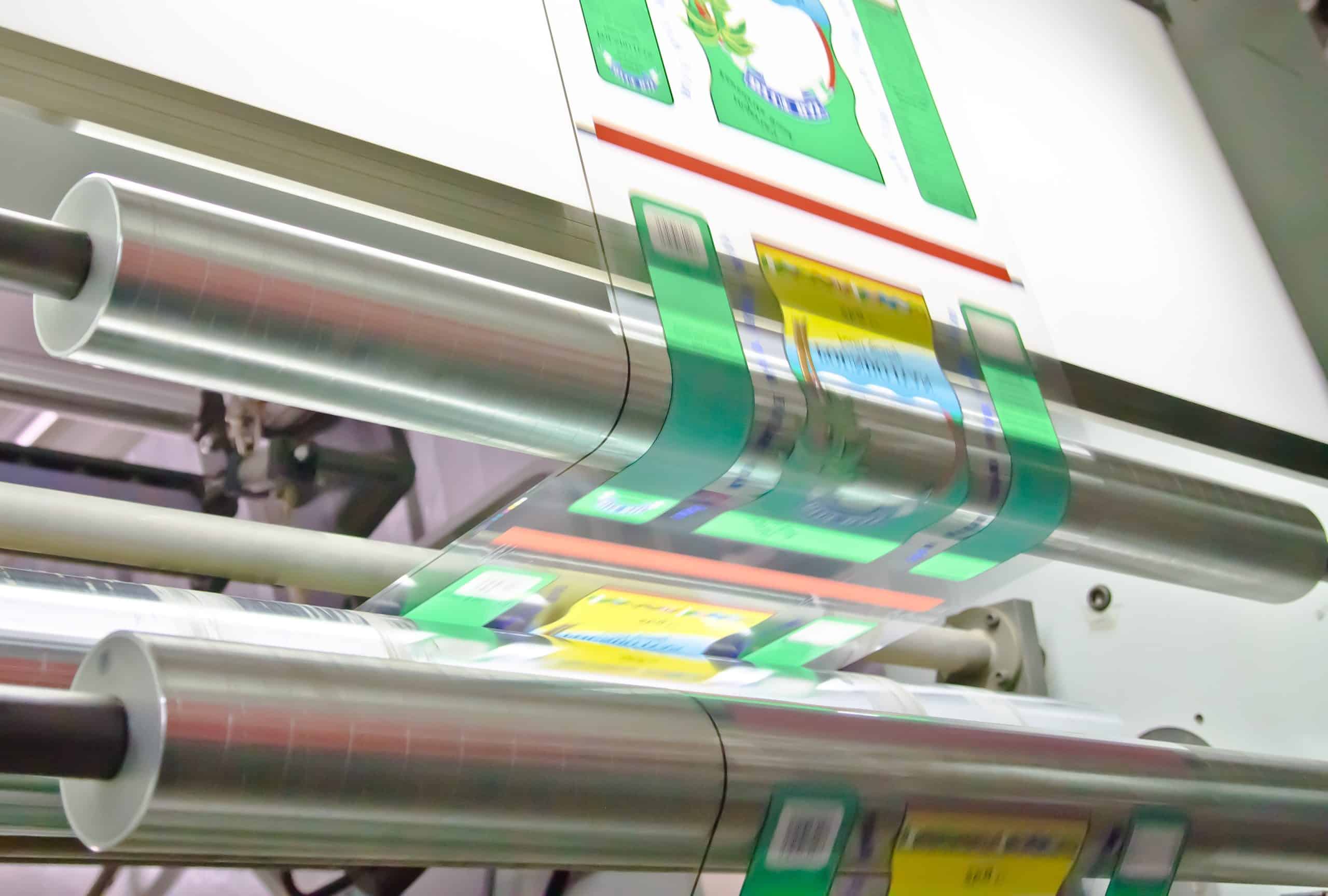
LENGLET IMPRIMEURS : 1€ to reduce your energy bill
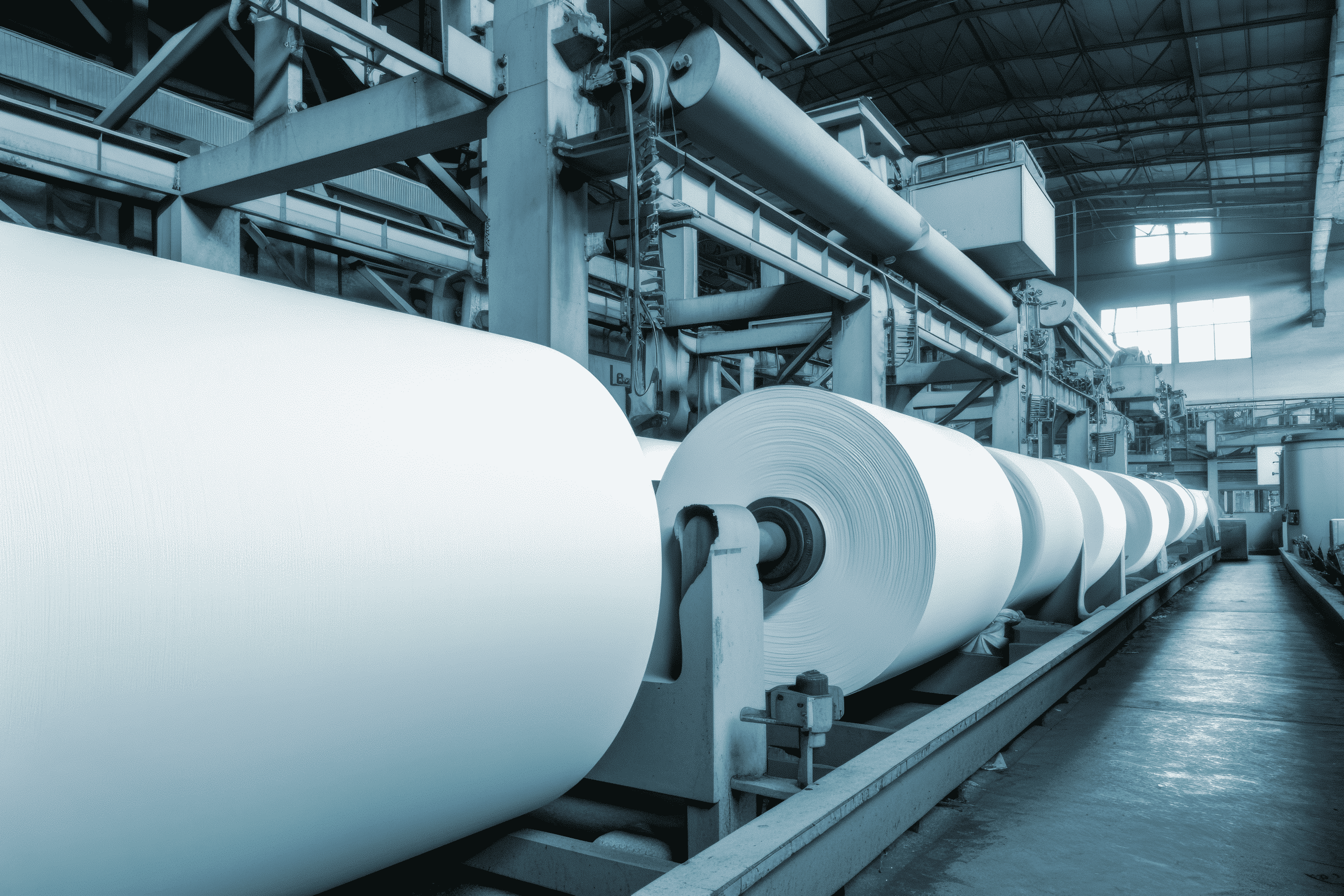
Modelling of the HTA/BT electric network
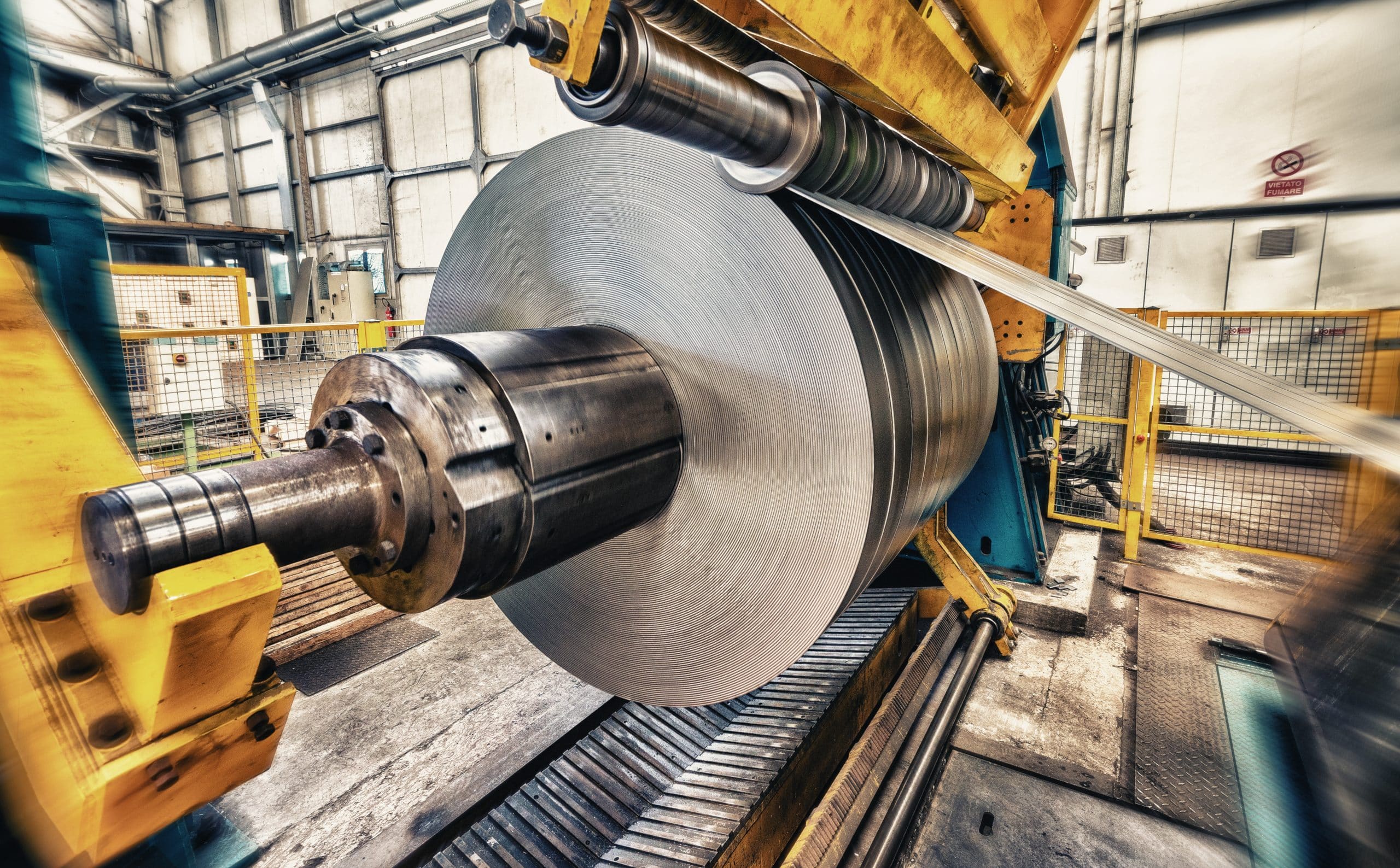
Fiabilisation d’une ligne de décapage
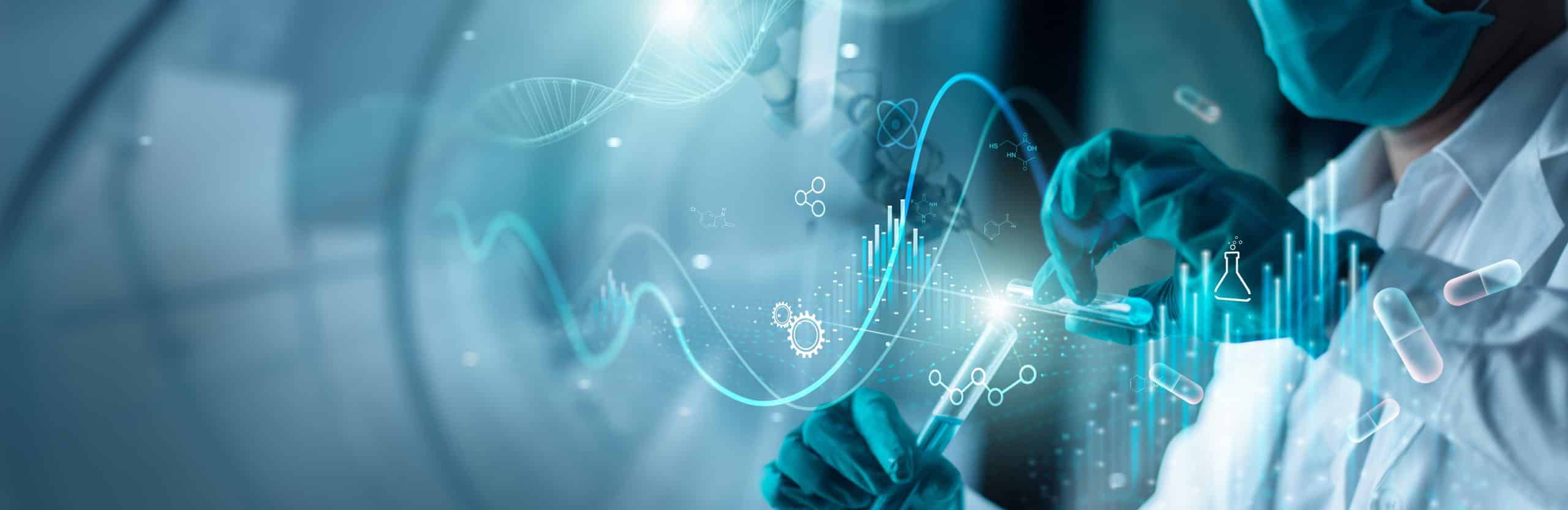
EMC analysis
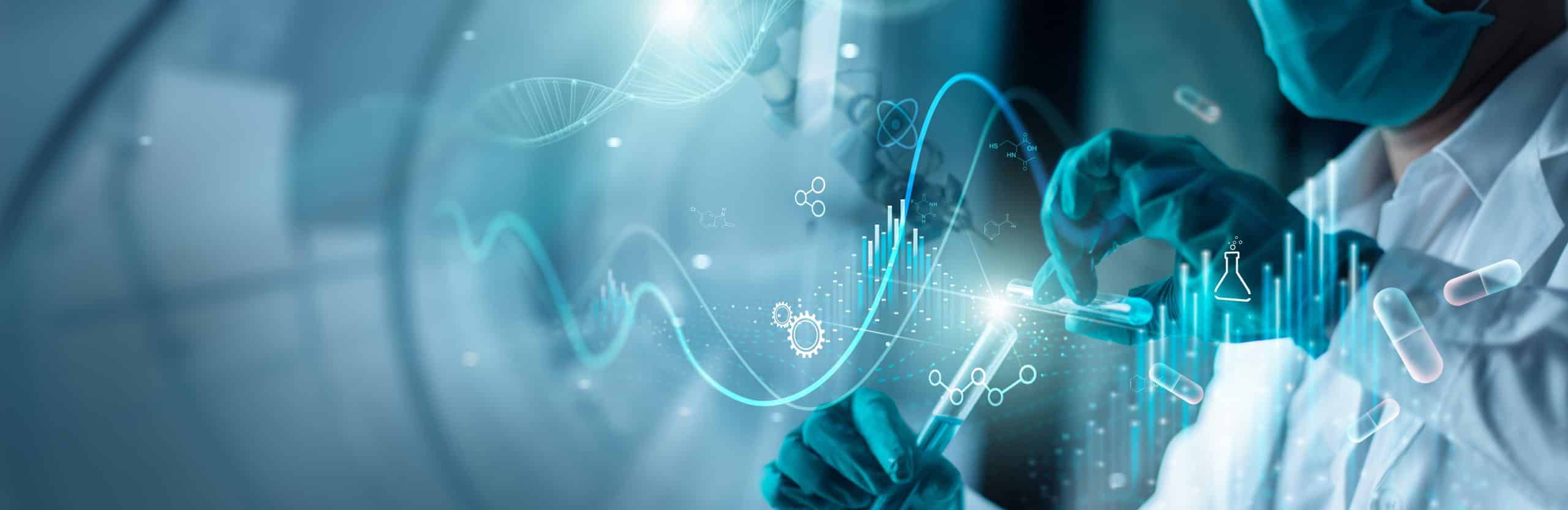
Modélisation réseau
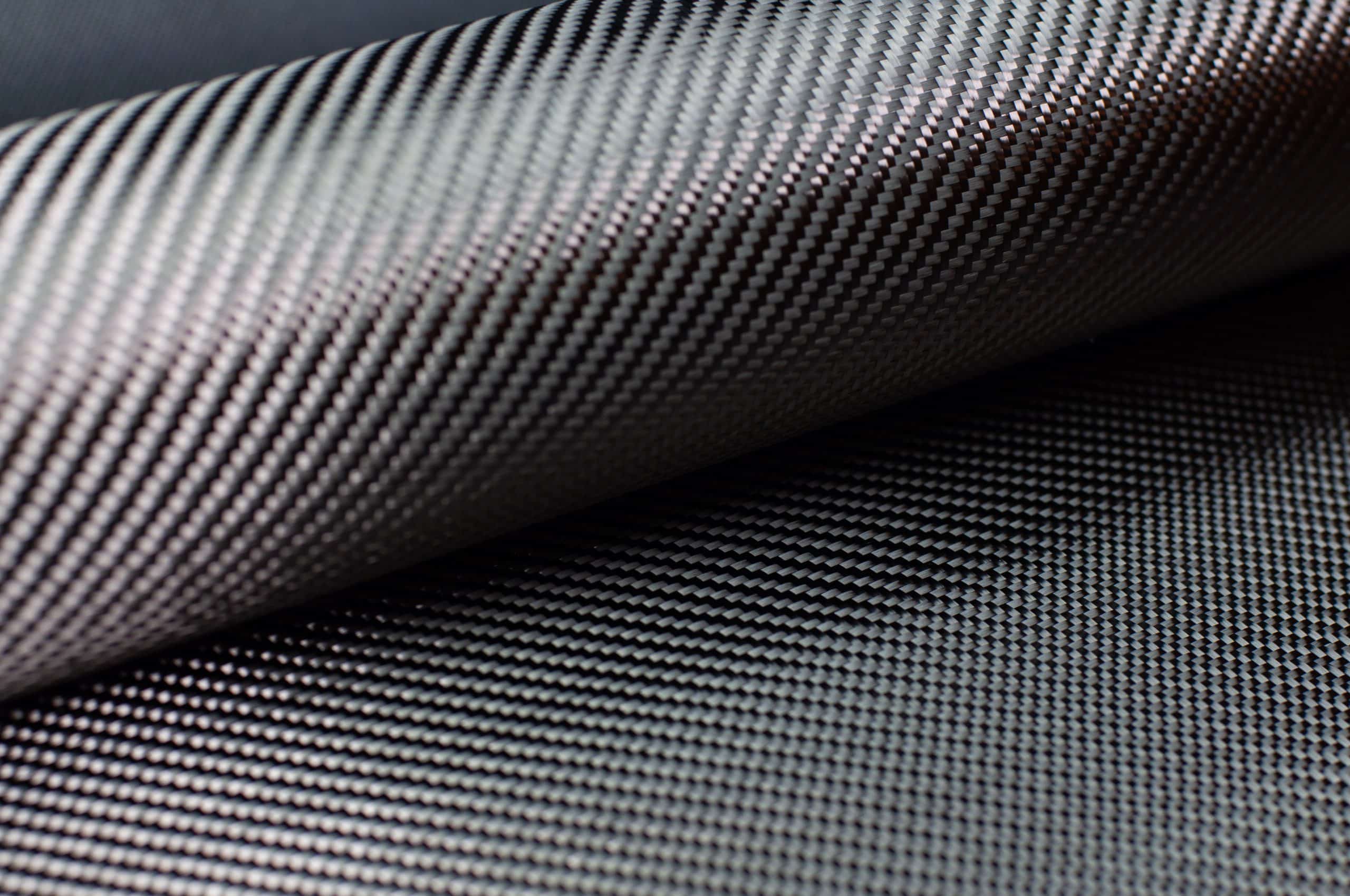
Reducer polymerizer vibration monitoring
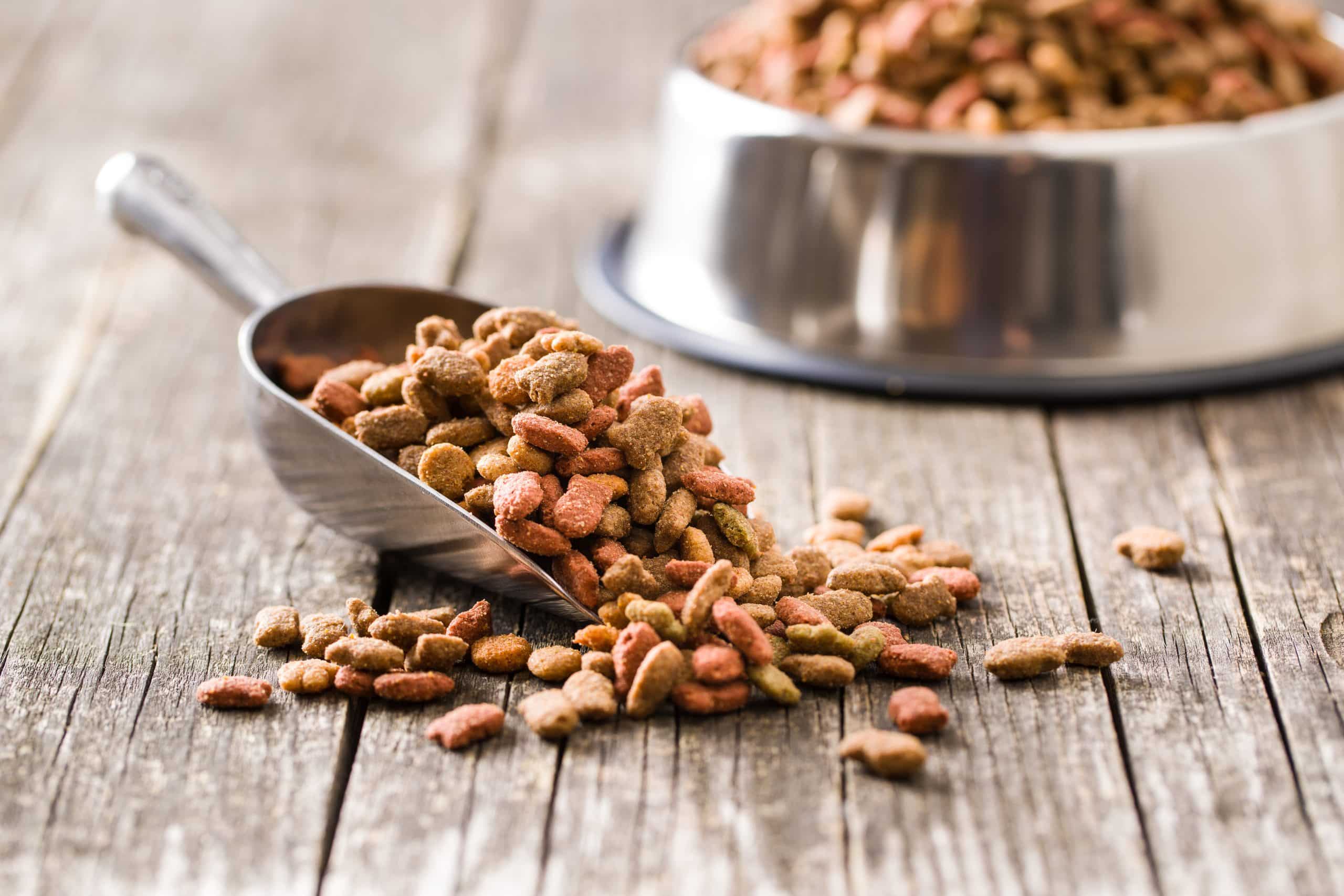
Maintenance method improvement project
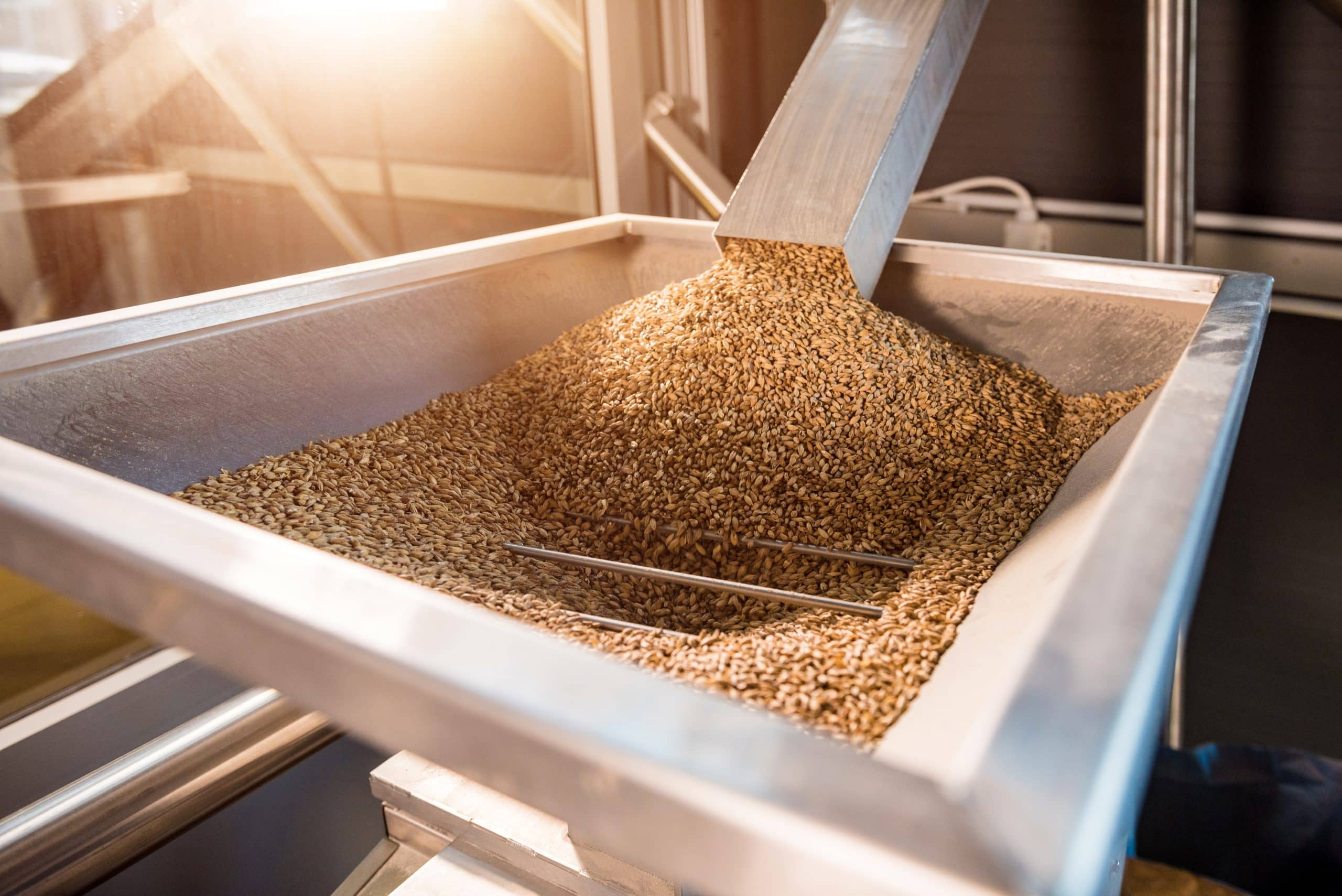
Contrat de mesures vibratoires
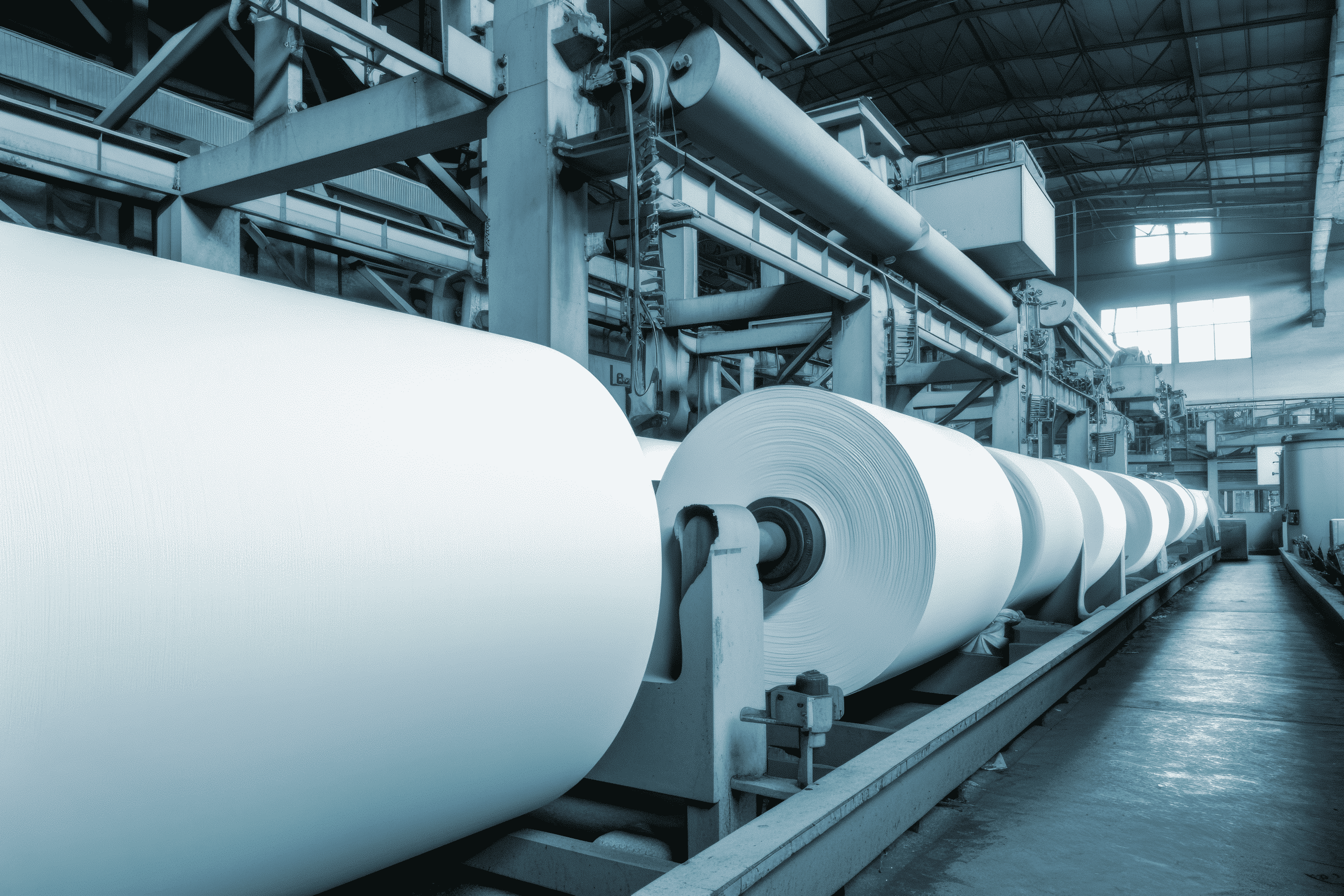
Contrat de suivi vibratoire
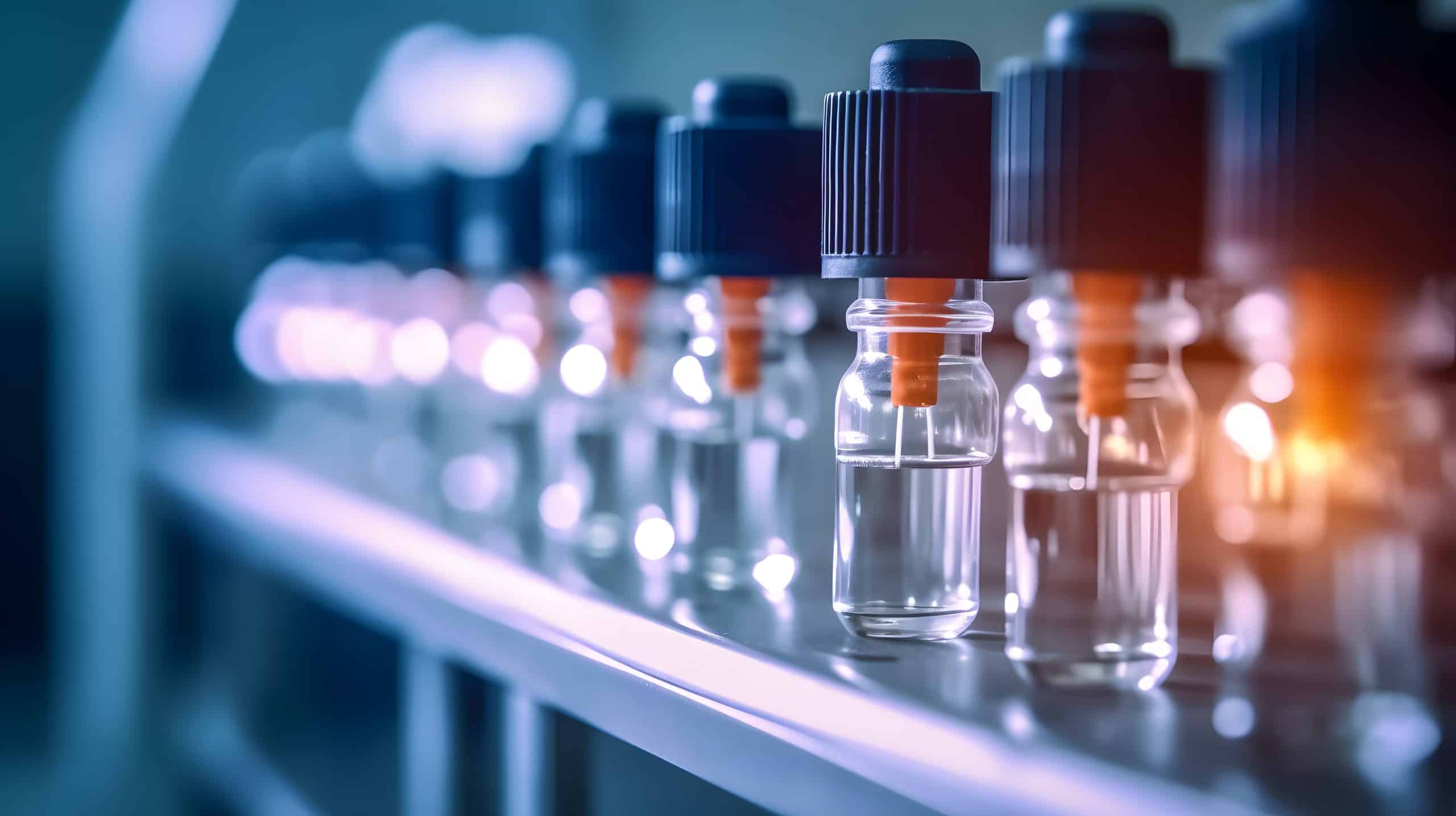
Contrôle par onde de choc de 46 moteurs asynchrones de 7,5KW (400V) à 750KW (5000V)
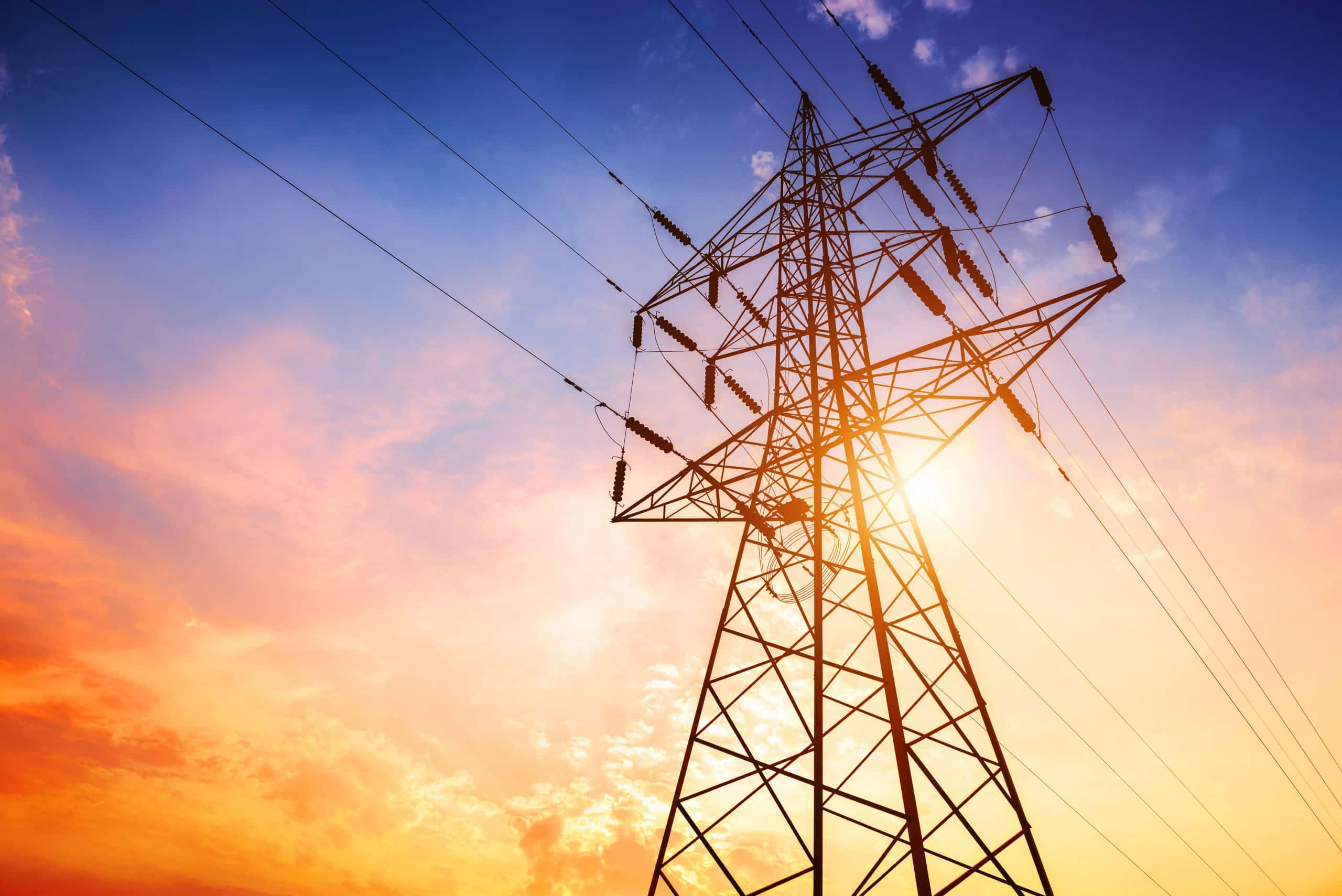
Remplacement de 4 CN obsolètes 810T par 1 CN Sinumerik 840D sl Siemens
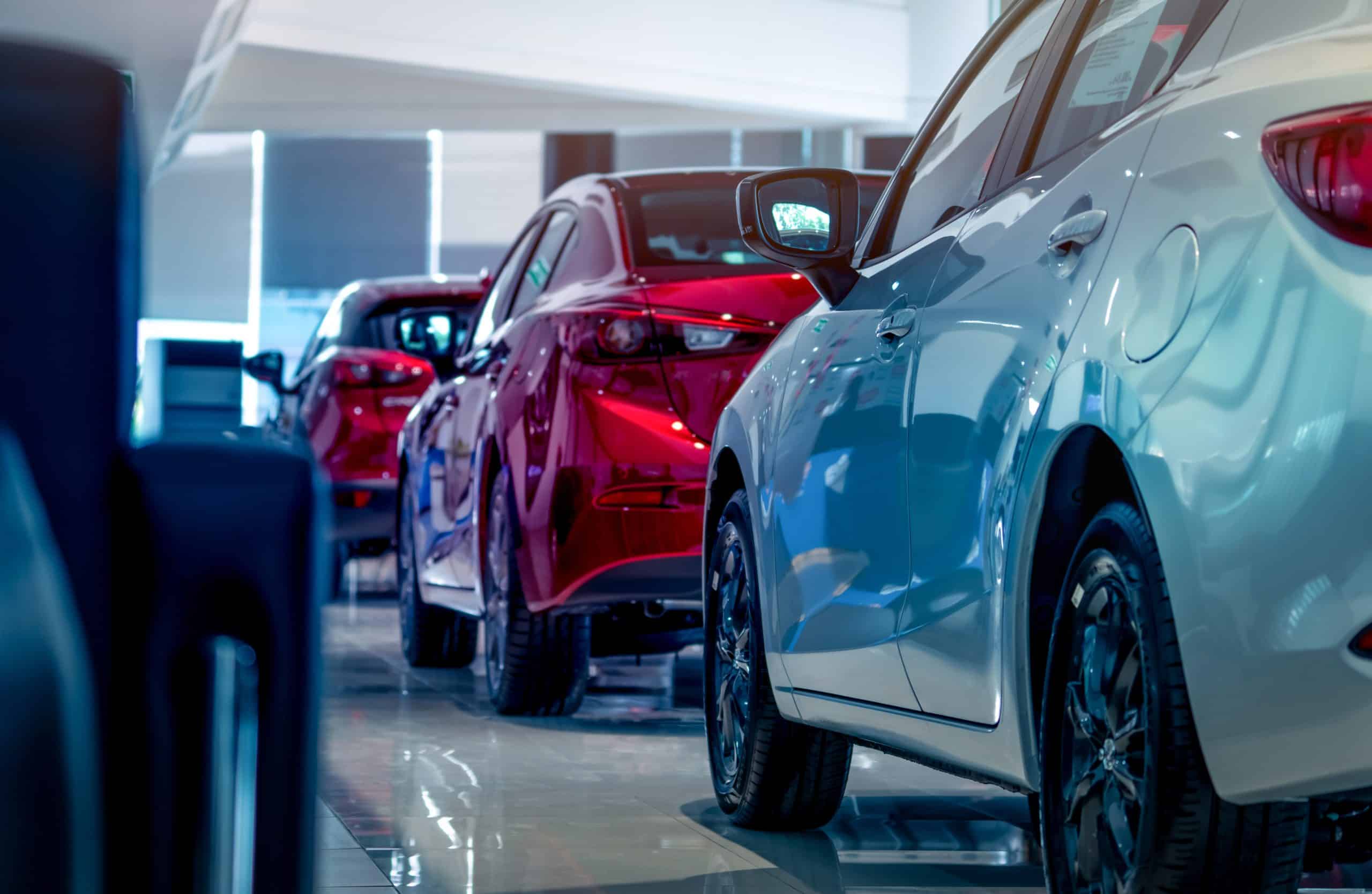
Modification îlot ZF
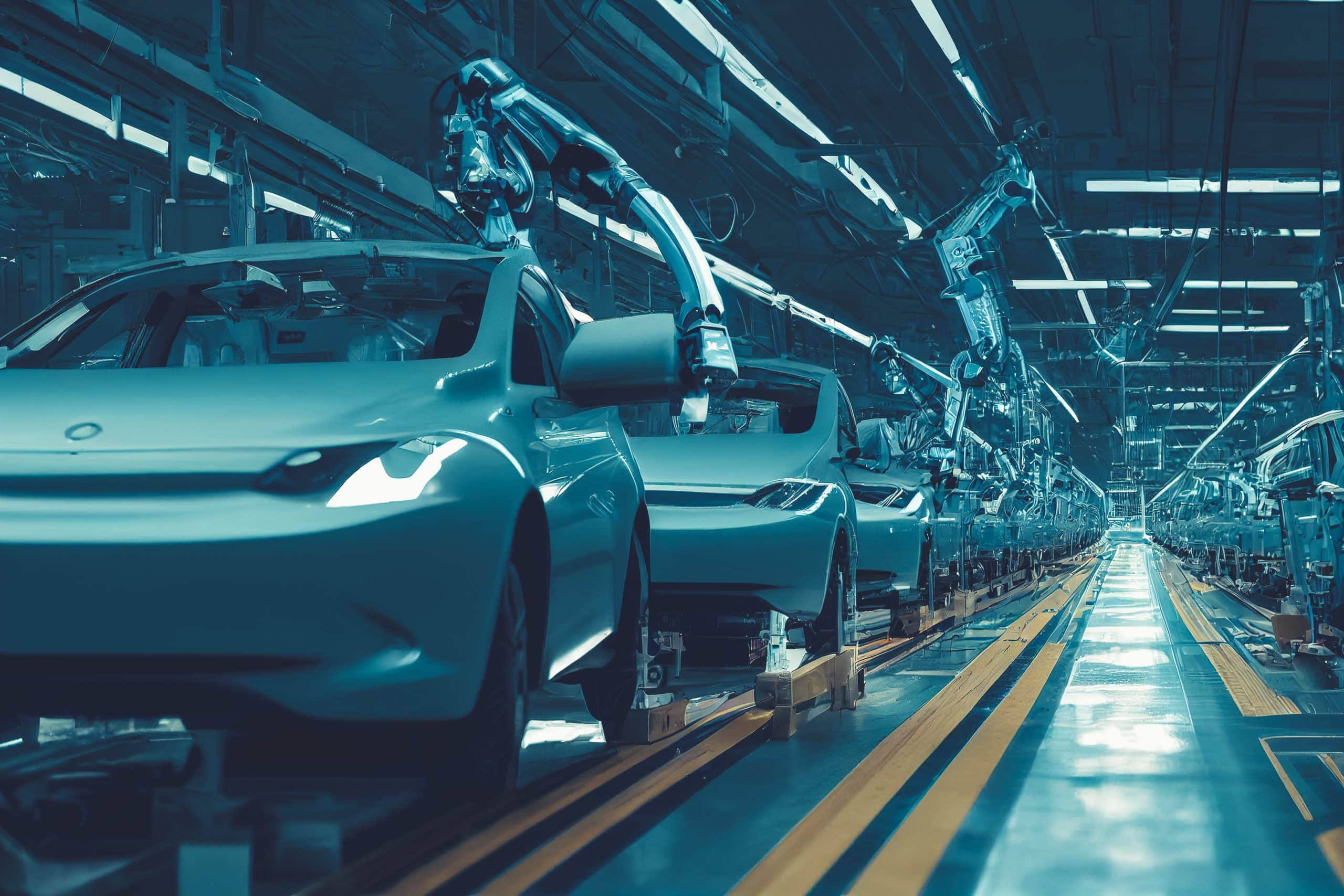
Remplacement robot presse
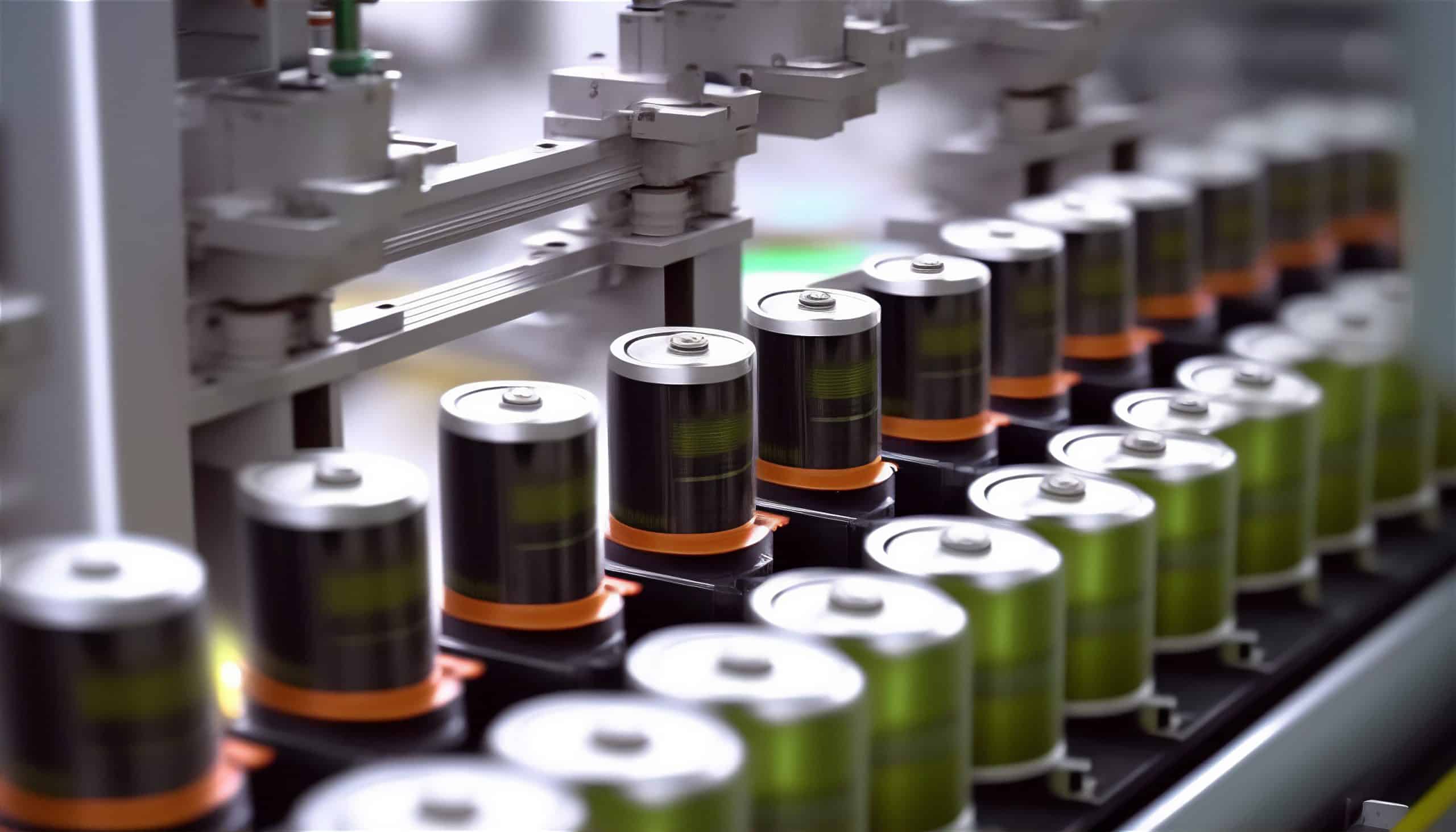
Cellule robotisée de dépose résine et convoyage d’une ligne d’emballage de batteries DAIMLER
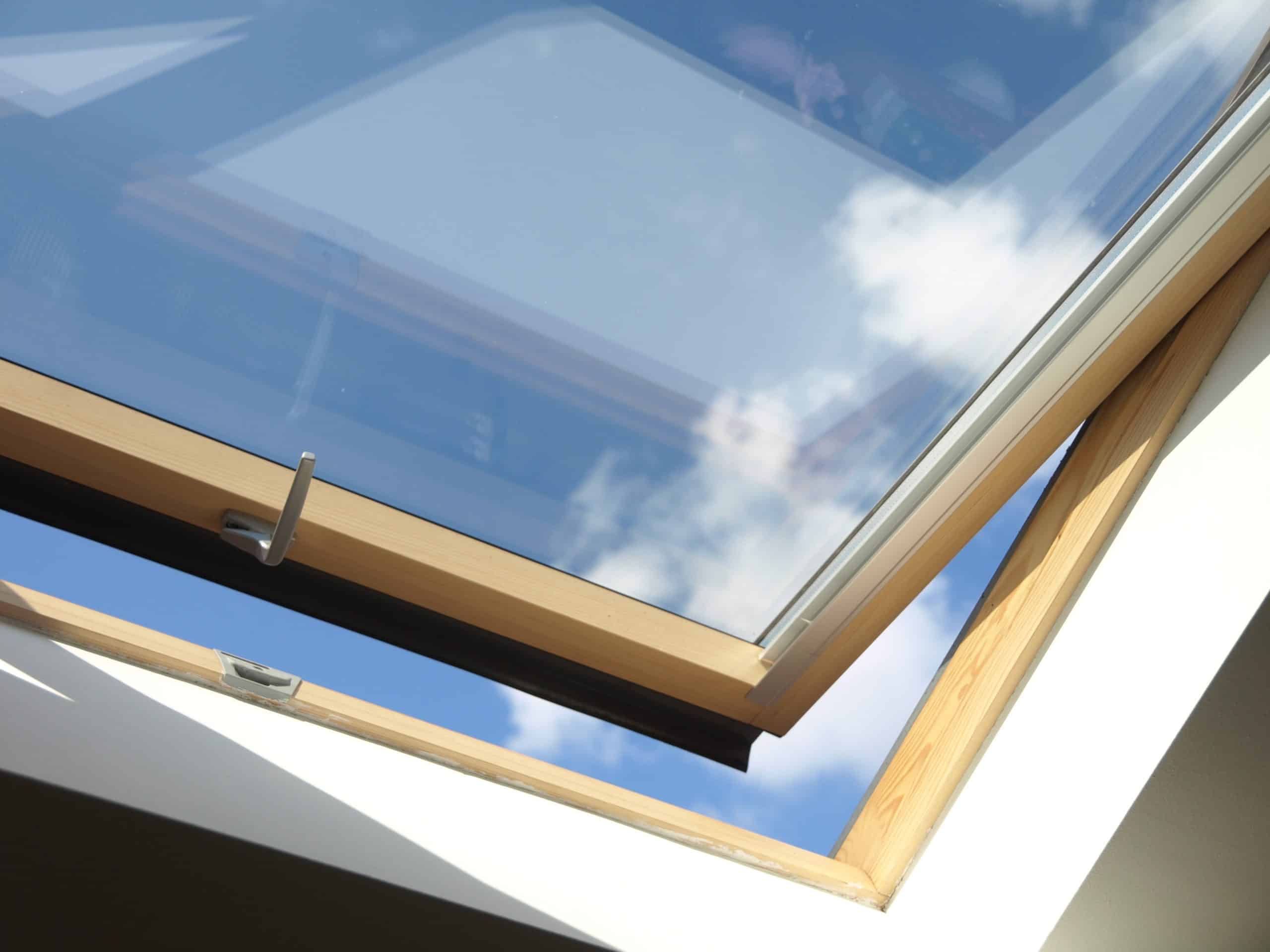
Robot de palettisation ligne peinture
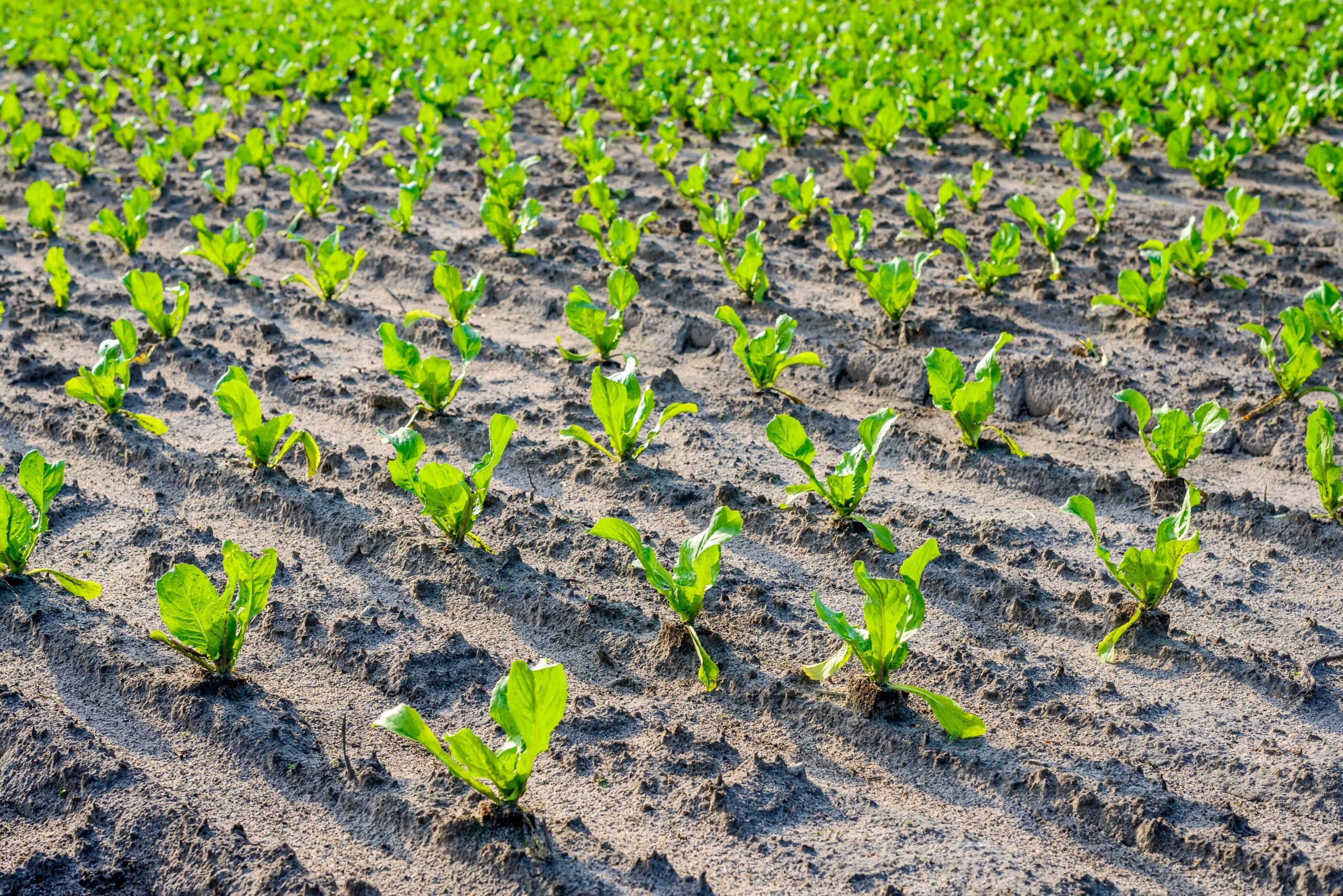
Robot de lavage de bacs à endives
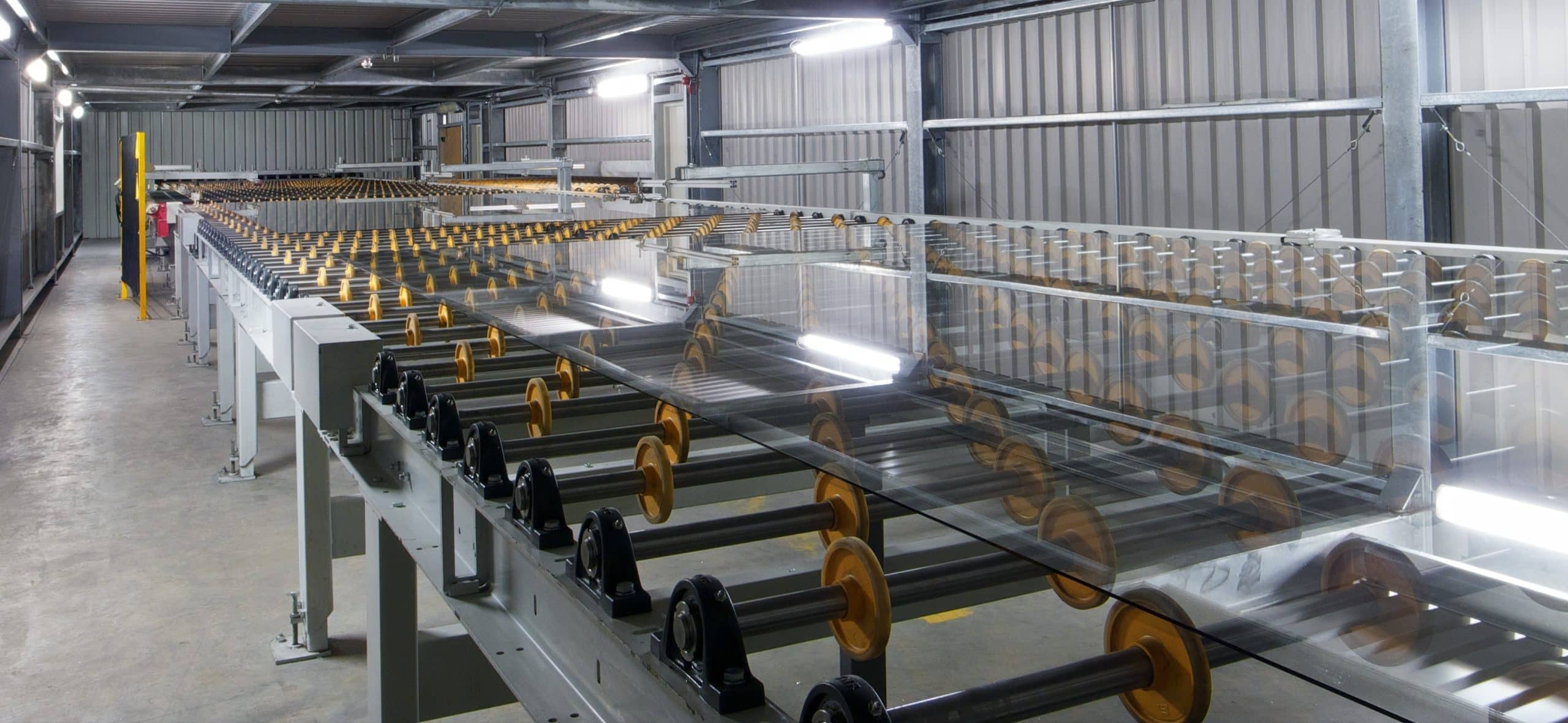
Digital Twin d’une nouvelle ligne de production
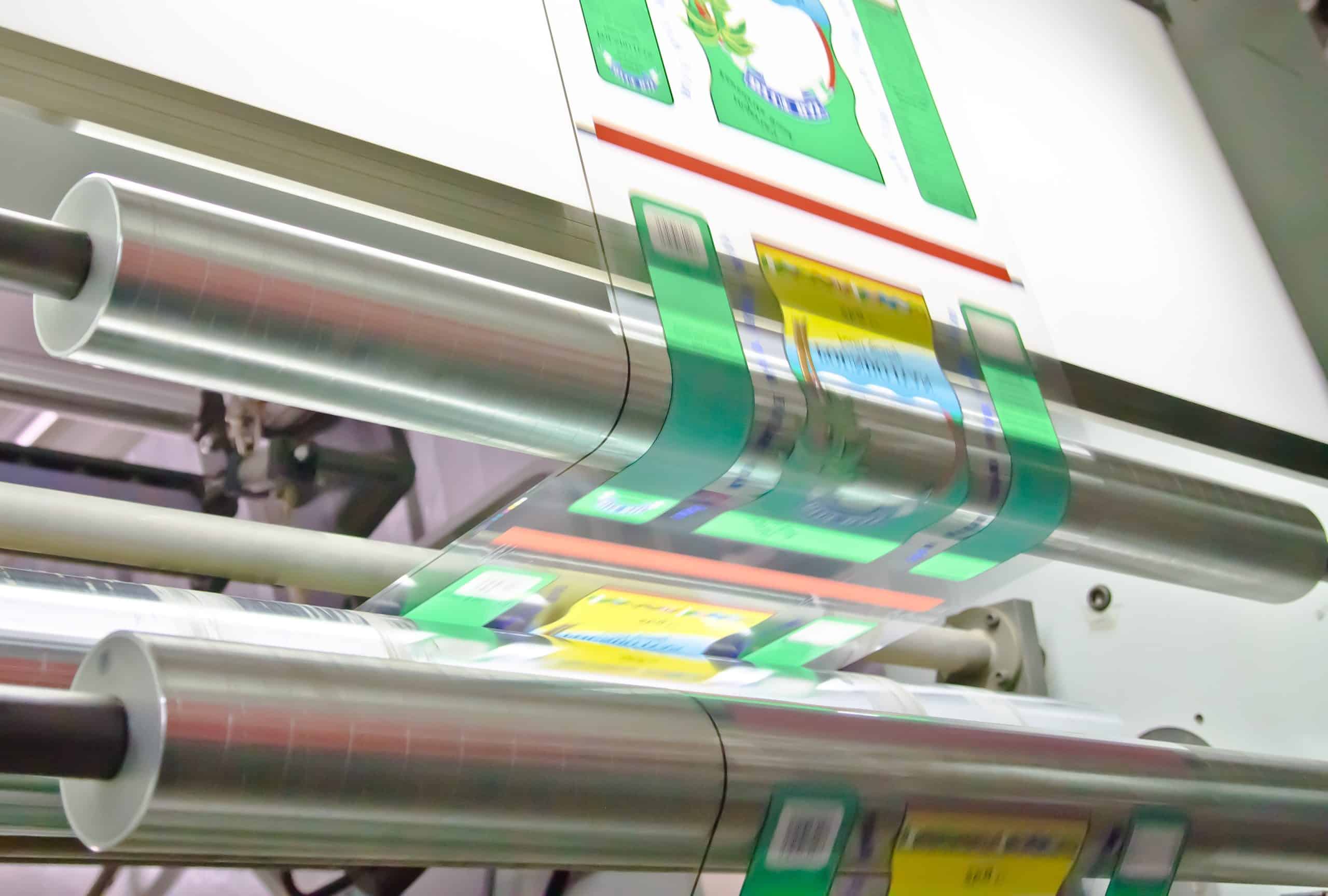
LENGLET IMPRIMEURS : Retrofit variateurs moteurs unités de récupération de solvant
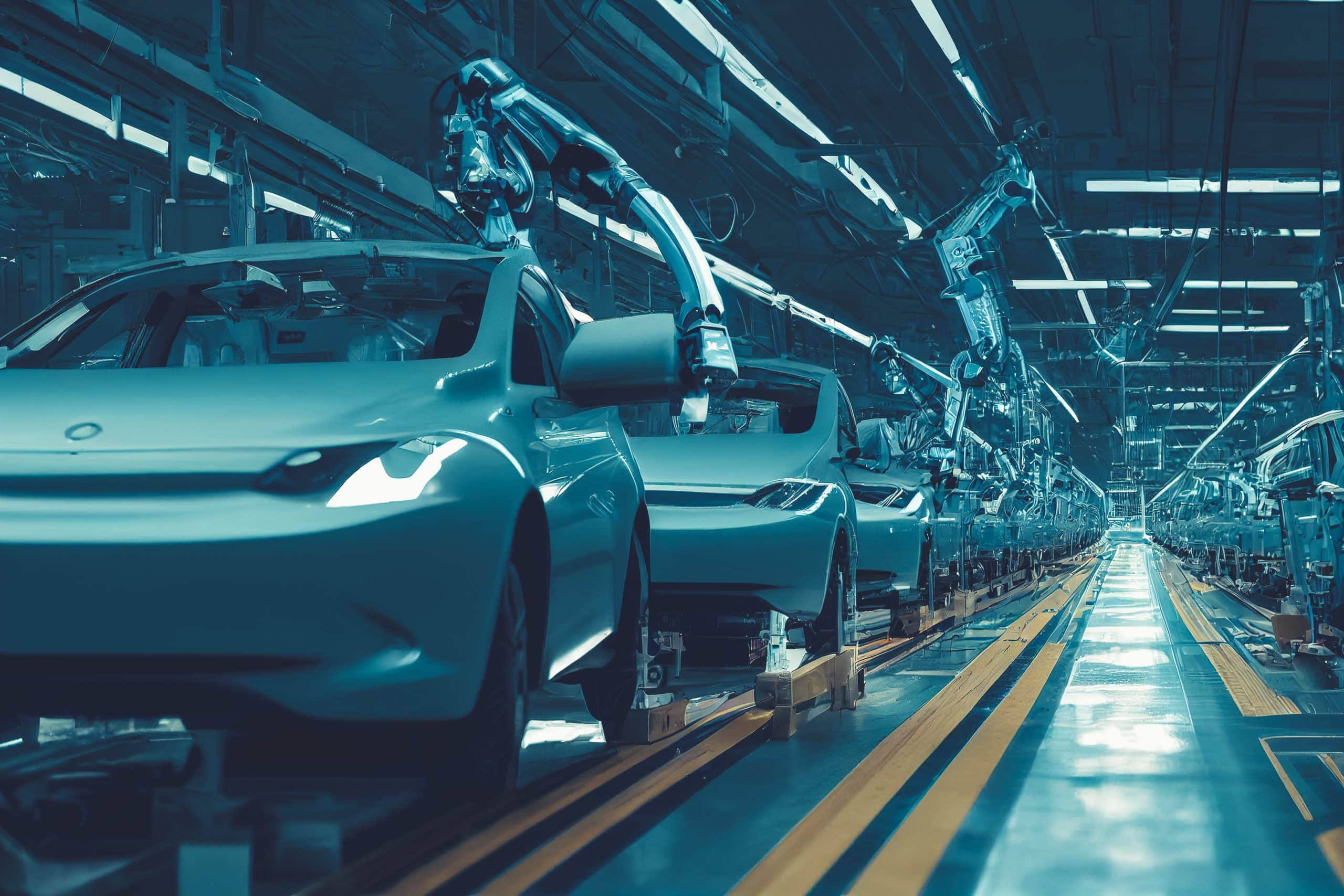
Rétrofit de l’électronique de puissance et de commande d’une ligne de découpe
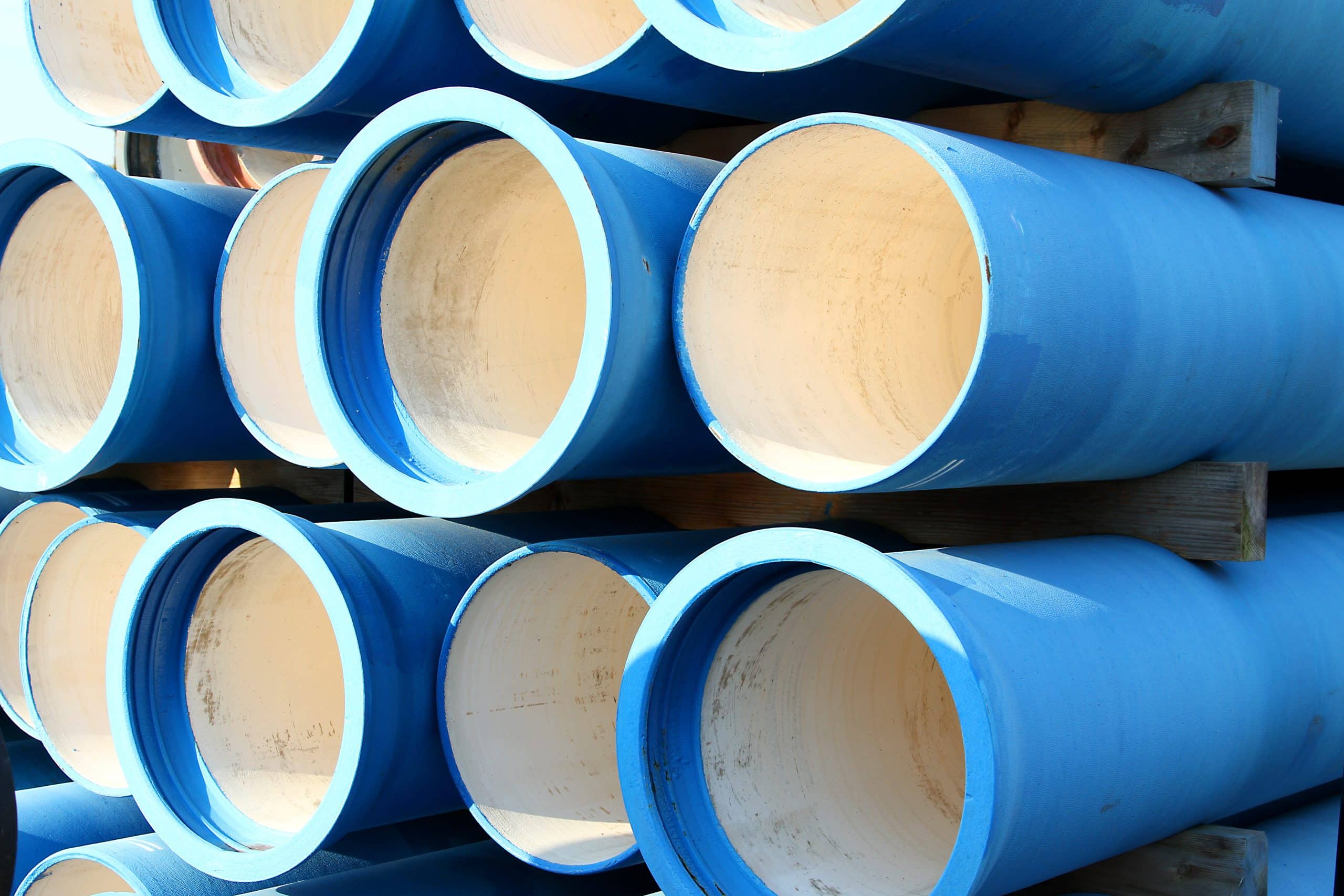
Rétrofit électrique pont HFX 16T
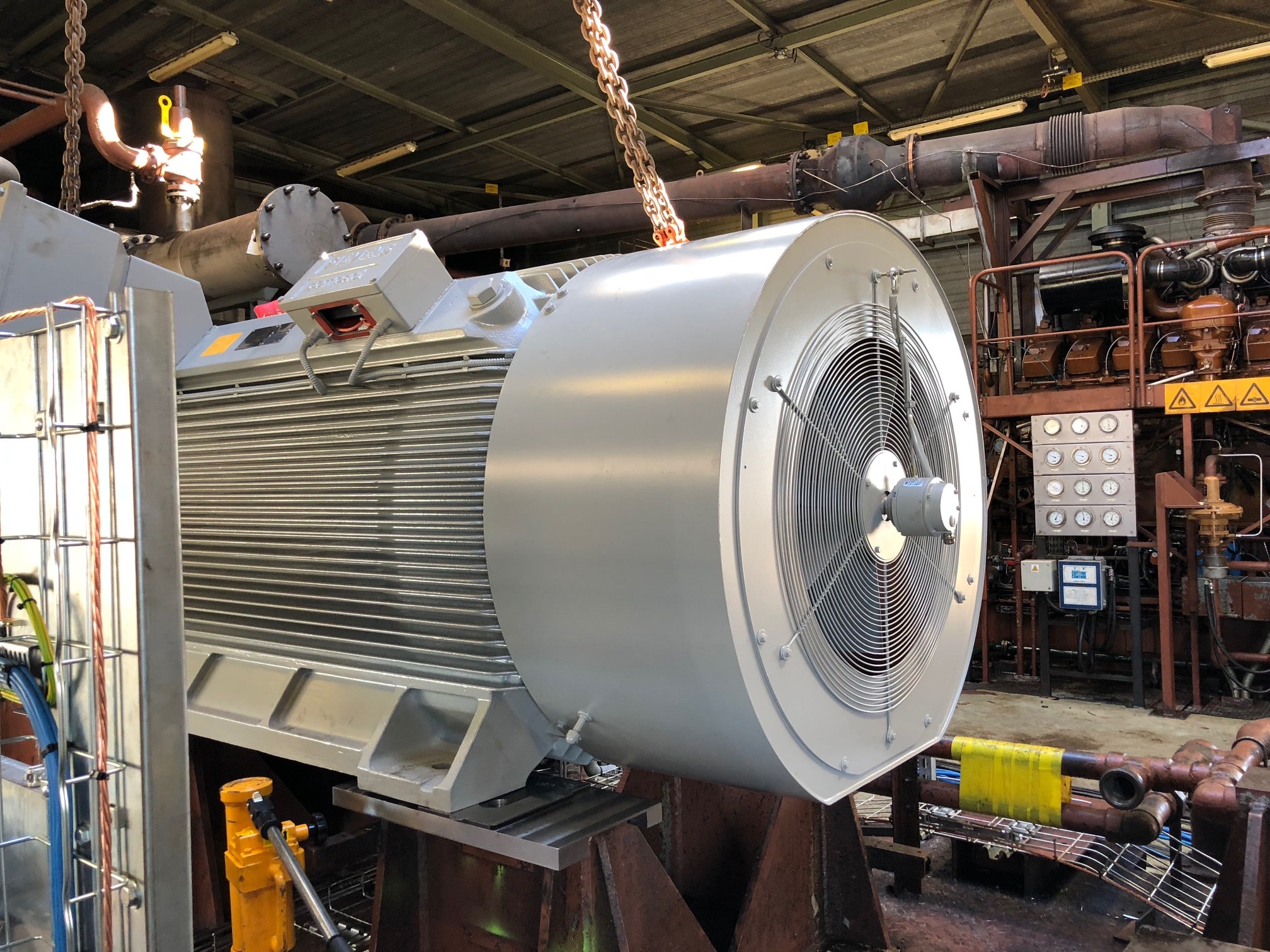
Motorisation of compressors in a colliery gas compression station
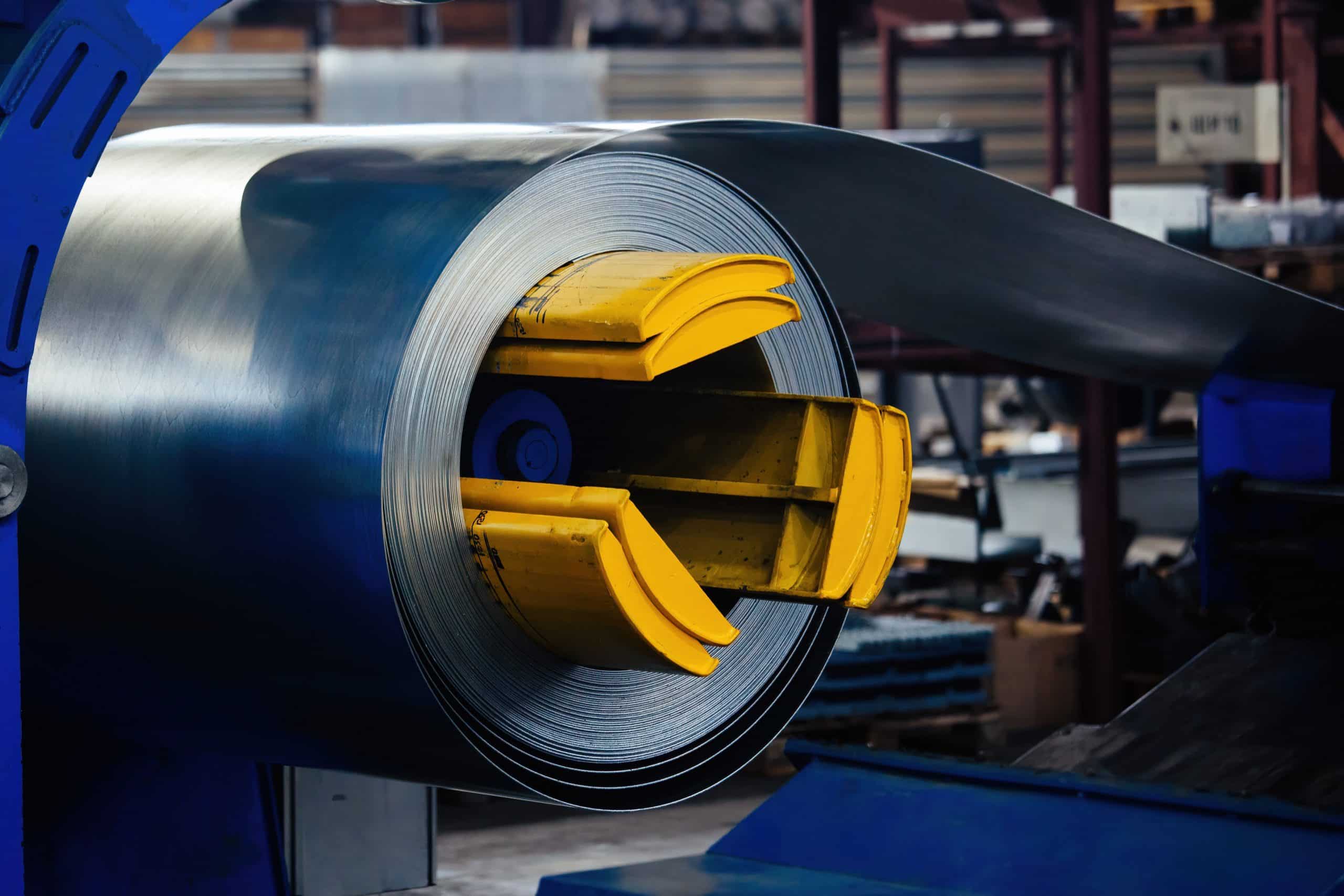
Obsolescence of the oven’s 7 CC ALSTHOM drives
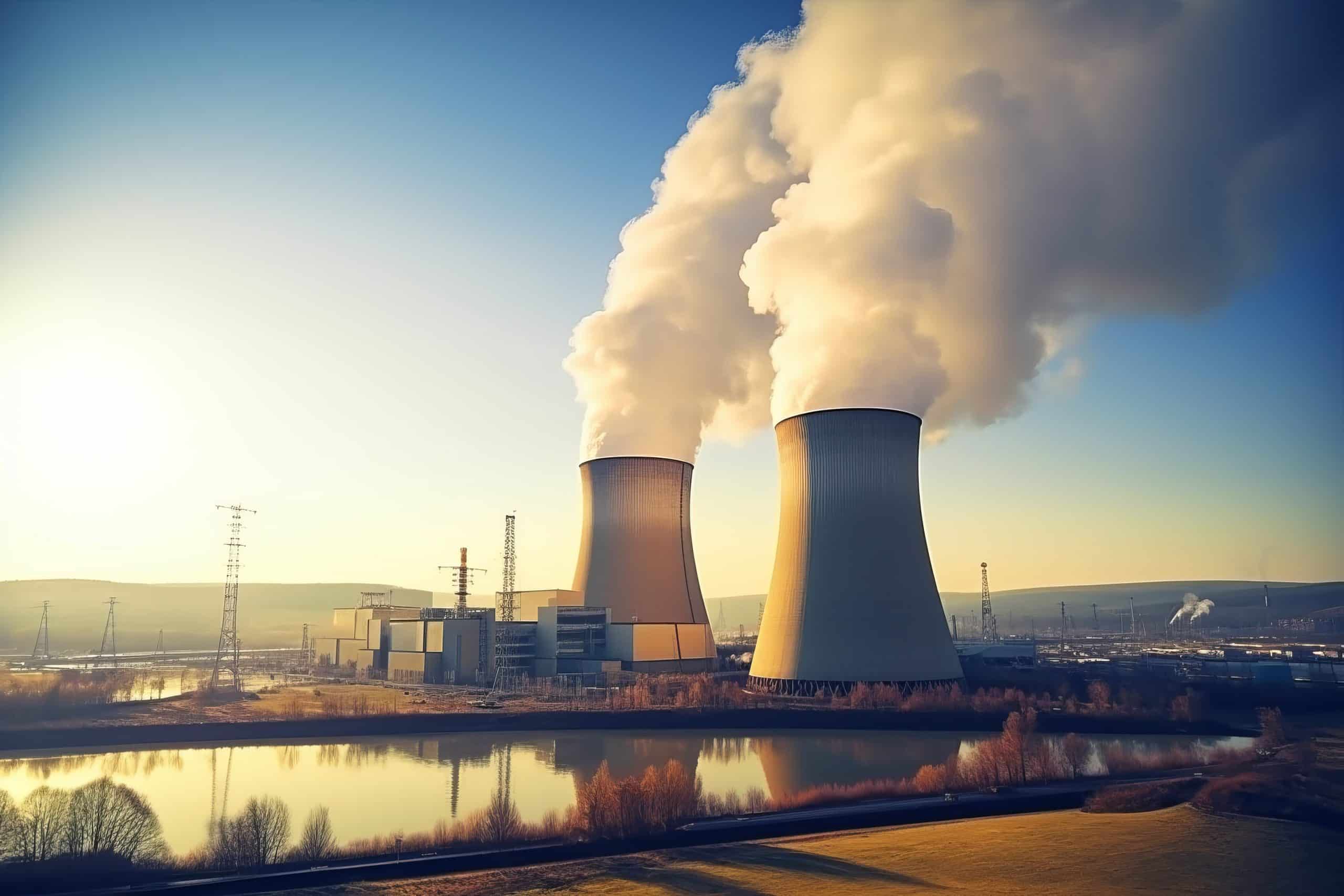
Retrofitting of an impressive balancing bench
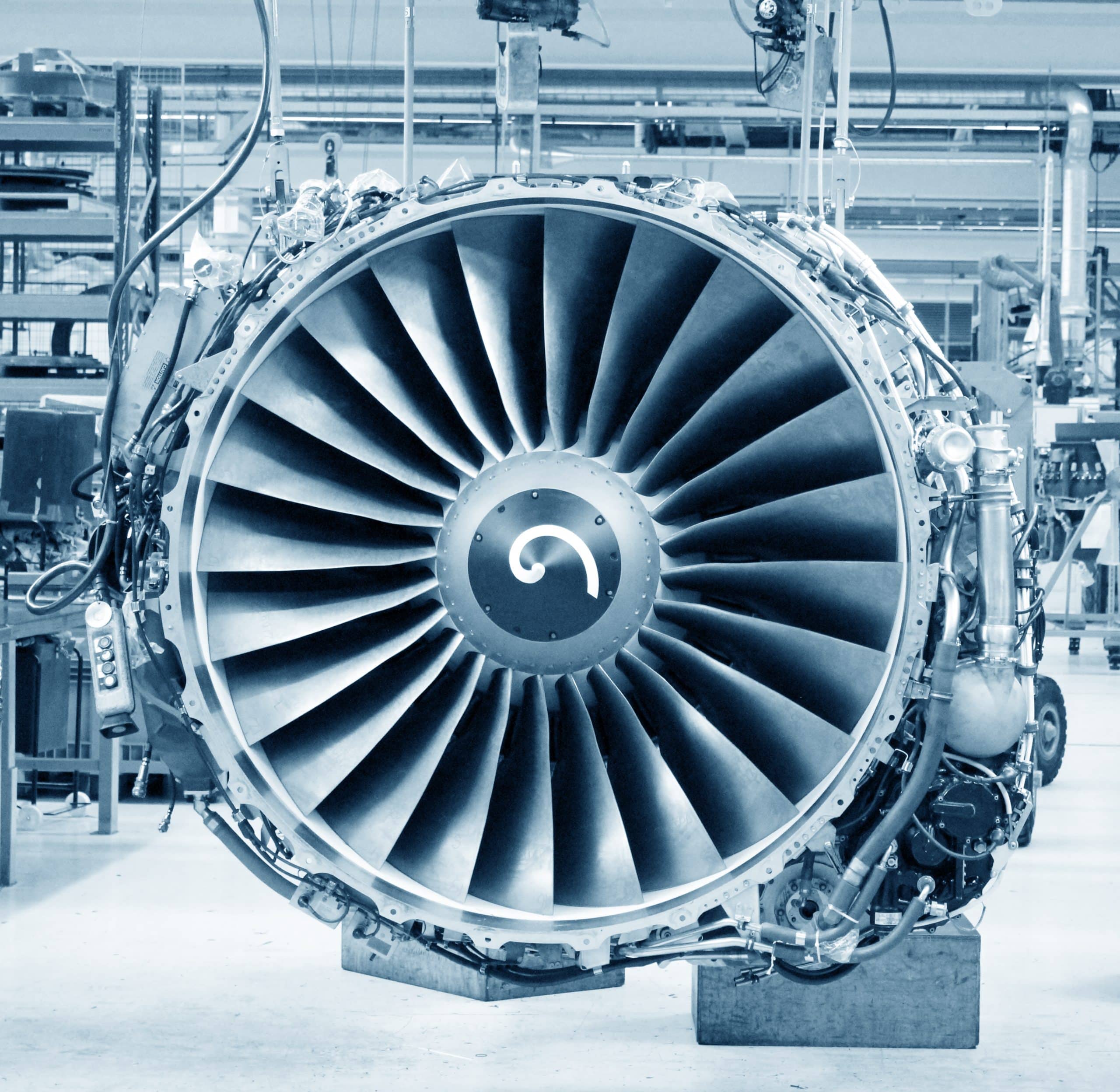
Retrofit of a machine for superfinishing machined parts
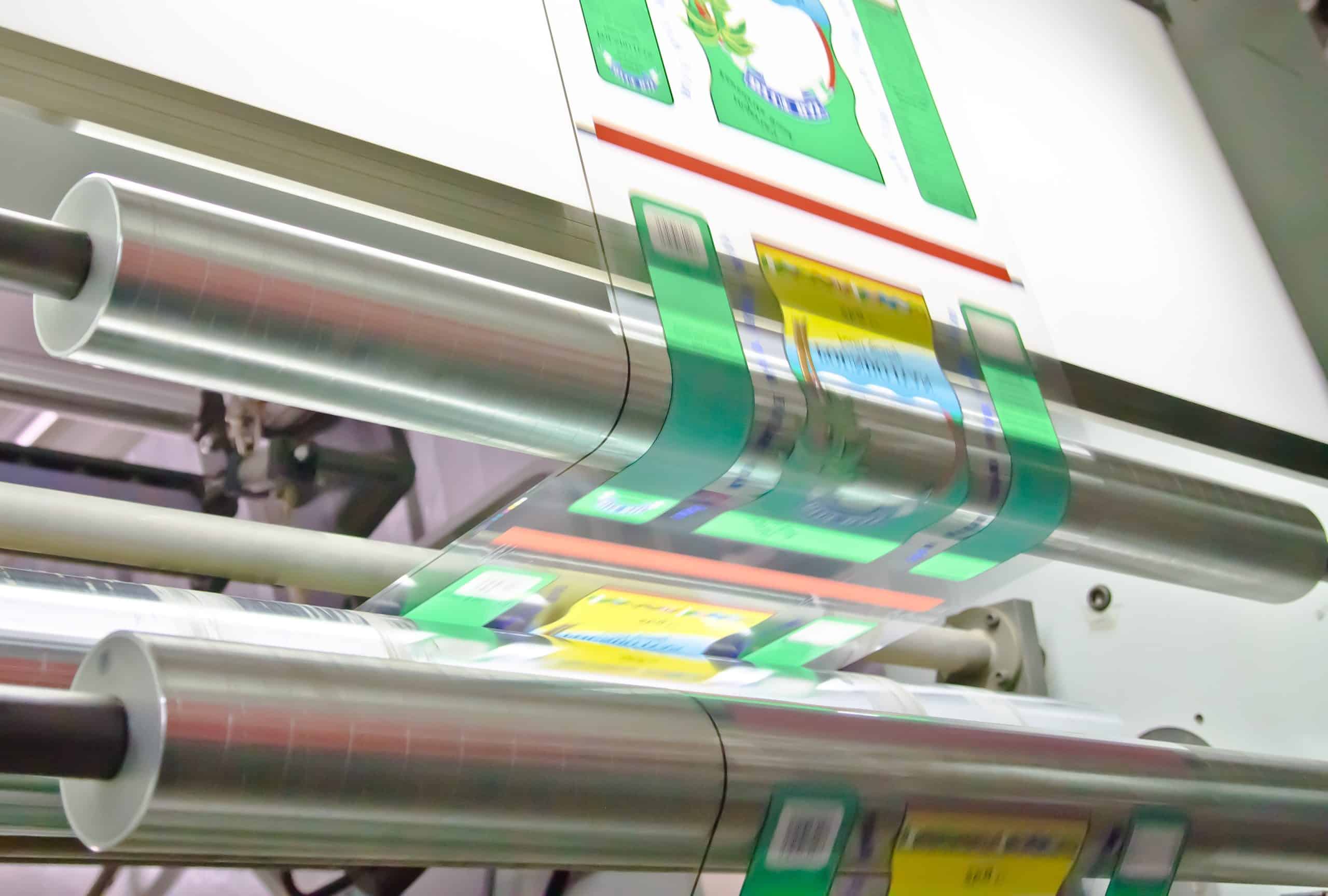
Retrofitting of the robotics part of a nine-colour printing line
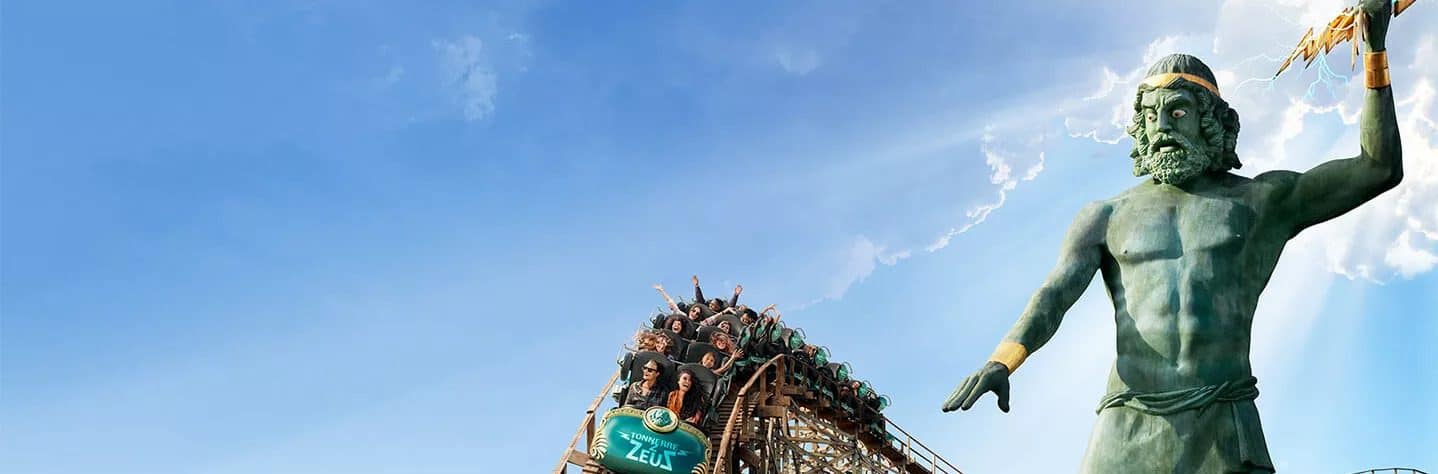