Maintenance method improvement project
Number of project hours: 40 hours
Project duration: 6 months
Customer expectations
Our customer called on DV GROUP’s expertise to improve its maintenance strategy. Indeed, it takes a minimum of 3 days to change a mill bearing during planned maintenance or in the event of unplanned breakdowns, resulting in major production stoppages. What’s more, the 2 annual vibration measurement campaigns are not enough to control unexpected breakdowns (bearing cage failure, lubrication failure, etc.).
Our customer’s objective is therefore to reduce maintenance downtime, and ensure 24/7 monitoring of the drive, by implementing a monitoring solution that can be deployed in the plant for other critical applications.
Translated with DeepL.com (free version)
DV GROUP Solution
To achieve these objectives, we offer our customer several solutions:
- An ENGINEERING solution with a study of the mechanical drive system
- A CONTROL solution for monitoring during commissioning
- An Electromechanical MAINTENANCE solution for assistance during installation
Technical Zoom: Equipment used
Machine monitoring
Vibration monitoring solution using wireless sensor technology.
This solution consists of 2 parts:
- An electrical box placed close to the customer’s installation for data acquisition and reception, and a router with a 4G Sim card for Internet connectivity.
- Sensors mounted at various strategic points on the equipment. The sensors continuously measure the vibration of the machine and send the data to a platform for processing by the customer or by a DV GROUP expert.
During installation, DV GROUP’s vibration analyses set alert and alarm thresholds for vibration levels. When thresholds are exceeded, an e-mail alert is sent to the customer and our technical support.
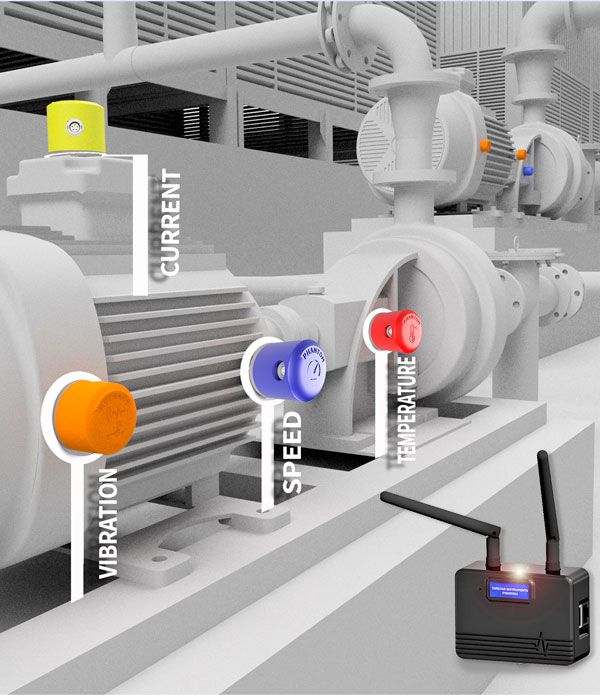
Machine monitoring
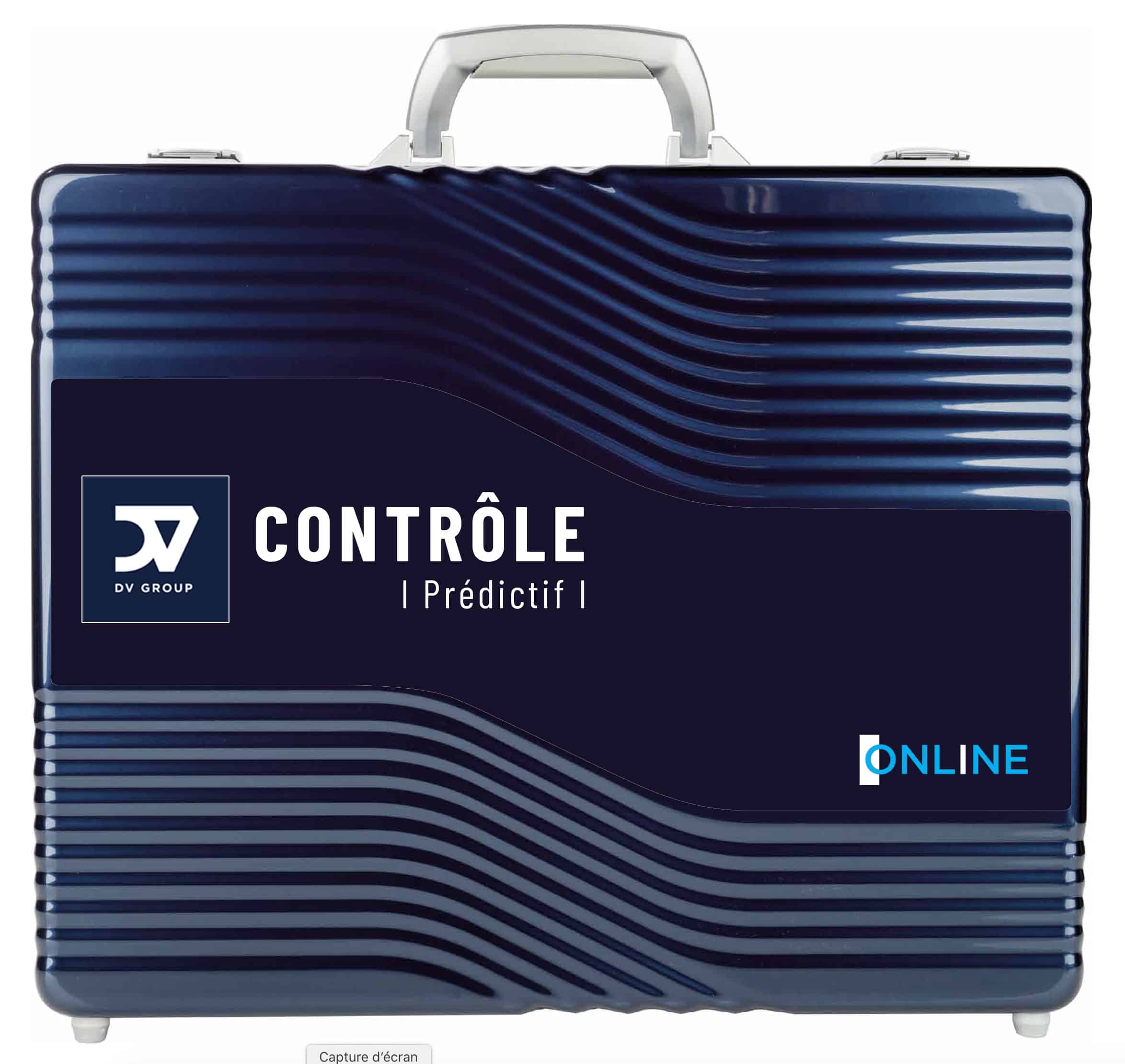
Customer benefits
- 3-day maintenance operation reduced to an 8-hour shift
- Automatic lubrication reduced by a factor of 4
- Bearing temperature reduced to 40°C instead of the initial 70°C
- Instant reaction and analysis time in case of drift
- Test on a mill validated, the solution will be deployed on other customer process equipment (extruders, ventilation, etc.).