Overhaul of an extruder reducer with 2 indexed output shafts
Client expectation
Given the importance of the co-extruder in their manufacturing process, a French plasticisation company wished to entrust to us the overhaul of the only reducer they had in stock in order to guard against a possible mechanical breakdown.
DV GROUP Solution
In fact, a breakdown of the co-extruder would systematically lead to the stoppage of half of production and as the lead time for the supply of a new reducer would be extremely long, out client could not afford not to have a product in stock. In order to be totally worry-free regarding the condition of the only reducer they had in stock, it was imperative to overhaul it.
Work carried out
DV GROUP technical solution:
3D printing of the shafts’ clamping matrix:
- Given the particularity of an extruder reducer with 2 indexed output shafts, we suggested to our client modelling and 3D-printing the shafts’ clamping matrix in order to guarantee their correct positioning during refitting.
Removal/refitting and overhauling of the reducer in the workshop:
- Visual monitoring of the product
- Measurement of the axial play in the gearing rows
- Benchmarking of the bearing references
- Visual appraisal of tooth spacing (search for the usual signs of deterioration of the teeth)
- Monitoring of the span of the teeth with an impression of the teeth on scotch tape
- Removal of the gearing rows
- Monitoring of the size and geometry of the shaft rows
- Magnetic particle inspection of the teeth
- Inspection of the key grooves and connector spokes by bleeding
- Inspection of the casing size
- Cleaning of the reducer and gearing rows
- Reassembly of all the bearings and joints
- Monitoring and adjustment of the span of the teeth and indexation
- Adjustment of the axial play in the gearing rows
- Reassembly of the cover, waterproofing and upper casing
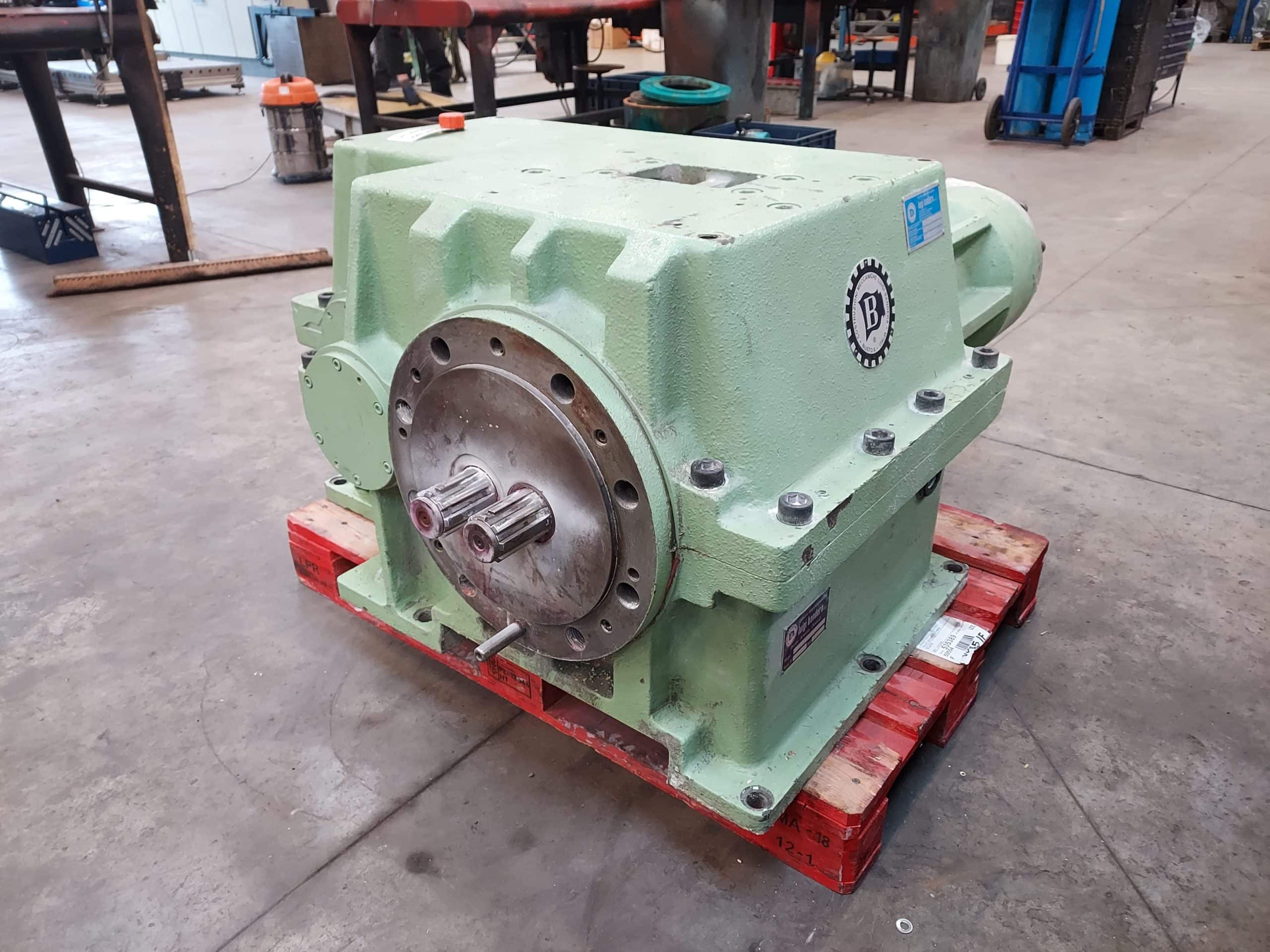
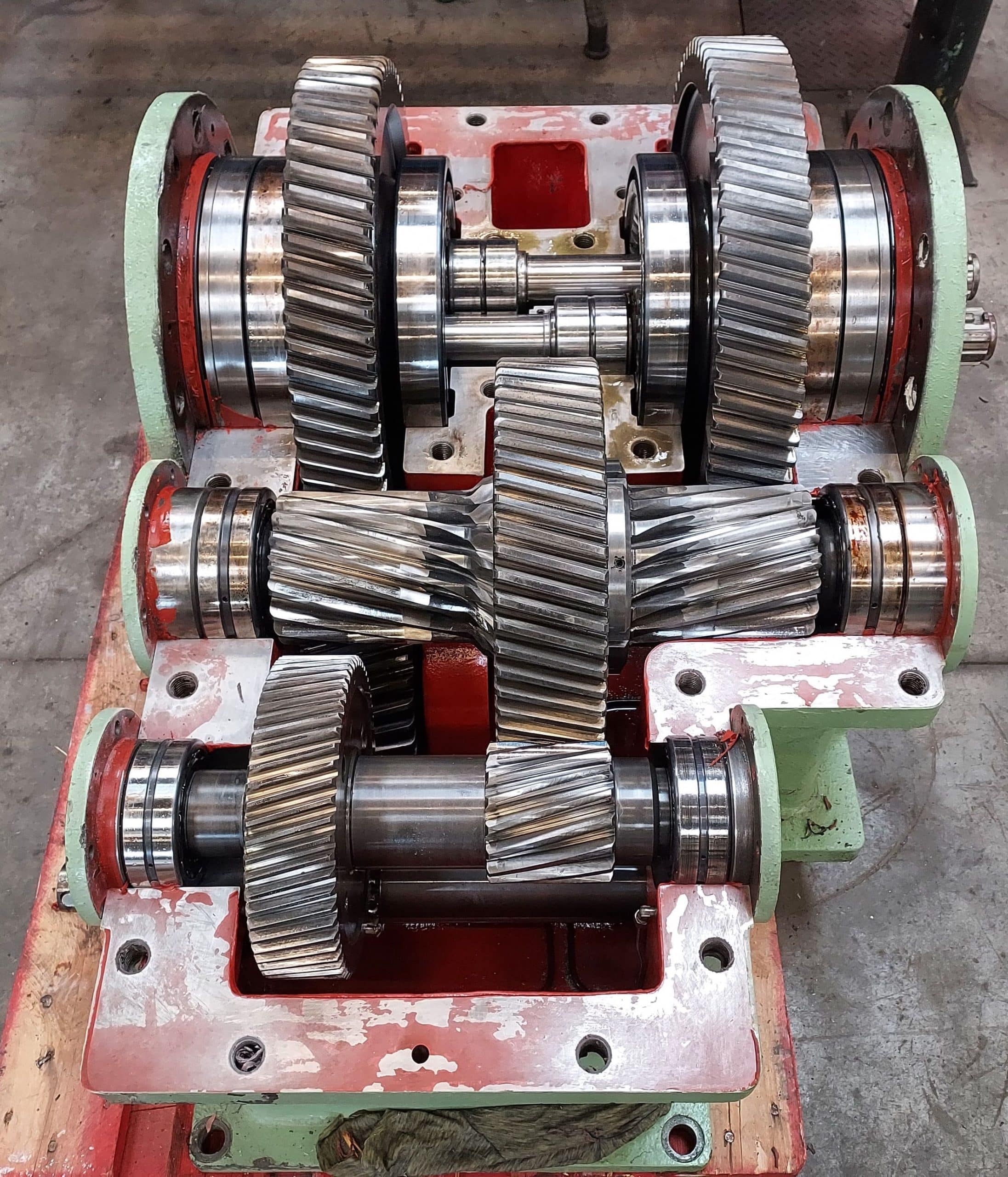