Projekt zur Verbesserung der Wartungsmethoden
Anzahl der Projektstunden : 40 Stunden
Dauer des Projekts : 6 Monate
Kundenerwartung
Unser Kunde nahm das Know-how von DV GROUP in Anspruch, um seine Wartungsstrategie zu verbessern. Für den Austausch eines Brecherlagers bei geplanten Wartungsarbeiten oder unvorhergesehenen Brüchen waren mindestens drei Tage erforderlich, was zu erheblichen Produktionsunterbrechungen führte. Außerdem war es bei den zwei jährlichen Schwingungsmesskampagnen nicht möglich, unerwartete Ausfälle zu beheben (Bruch des Lagerkäfigs, Ausfall der Schmierung usw.).
Das Ziel unseres Kunden war es daher, die Wartungsstillstandszeiten zu reduzieren und eine 24/7-Überwachung des Antriebs zu gewährleisten, indem eine Überwachungslösung eingerichtet wurde, die im Werk bei anderen wichtigen Anlagen eingesetzt werden kann.
Lösung der DV GROUP
Um diese Ziele zu erreichen, haben wir unserem Kunden mehrere Lösungen vorgeschlagen:
- Eine ENGINEERING-Lösung mit einem mechanischen Antrieb
- eine Online-ÜBERWACHUNG für die Überwachung ab dem Zeitpunkt der Installation
- Eine elektromechanische WARTUNGS-Lösung für die Unterstützung bei der Montage
Technisches detail: implementierte ausrüstung
- Überwachung der Maschine: Phantom-Lösung
Lösung zur Schwingungsüberwachung mit drahtlosen Sensoren.
Diese Lösung besteht aus zwei Teilen:
- Einem Schaltschrank in der Nähe der Anlage des Kunden, der die Erfassung und den Empfang von Daten ermöglicht, sowie einem Router mit einer 4G-Sim-Karte für die Internetverbindung.
- Sensoren, die an verschiedenen strategischen Punkten der Anlage angebracht sind. Die Sensoren messen permanent die Vibrationen der Maschine und senden die Daten an eine Plattform, so dass sie vom Kunden oder einem DV GROUP-Experten genutzt werden können.
Bei der Installation werden im Rahmen der DV-GROUP-Schwingungsanalyse die Alarm- und Warnschwellen für die Schwingungspegel festgelegt. Bei Überschreitung der Schwellenwerte wird eine E-Mail an den Mandanten und unseren technischen Support gesendet.
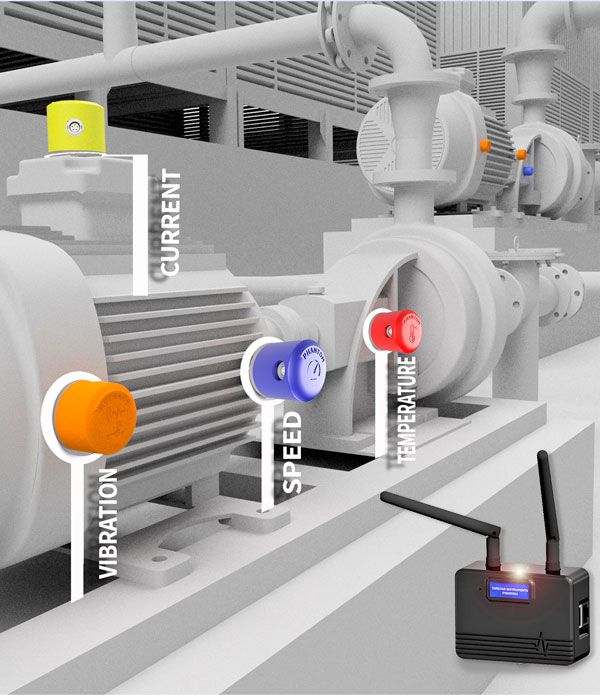
Maschinenüberwachung
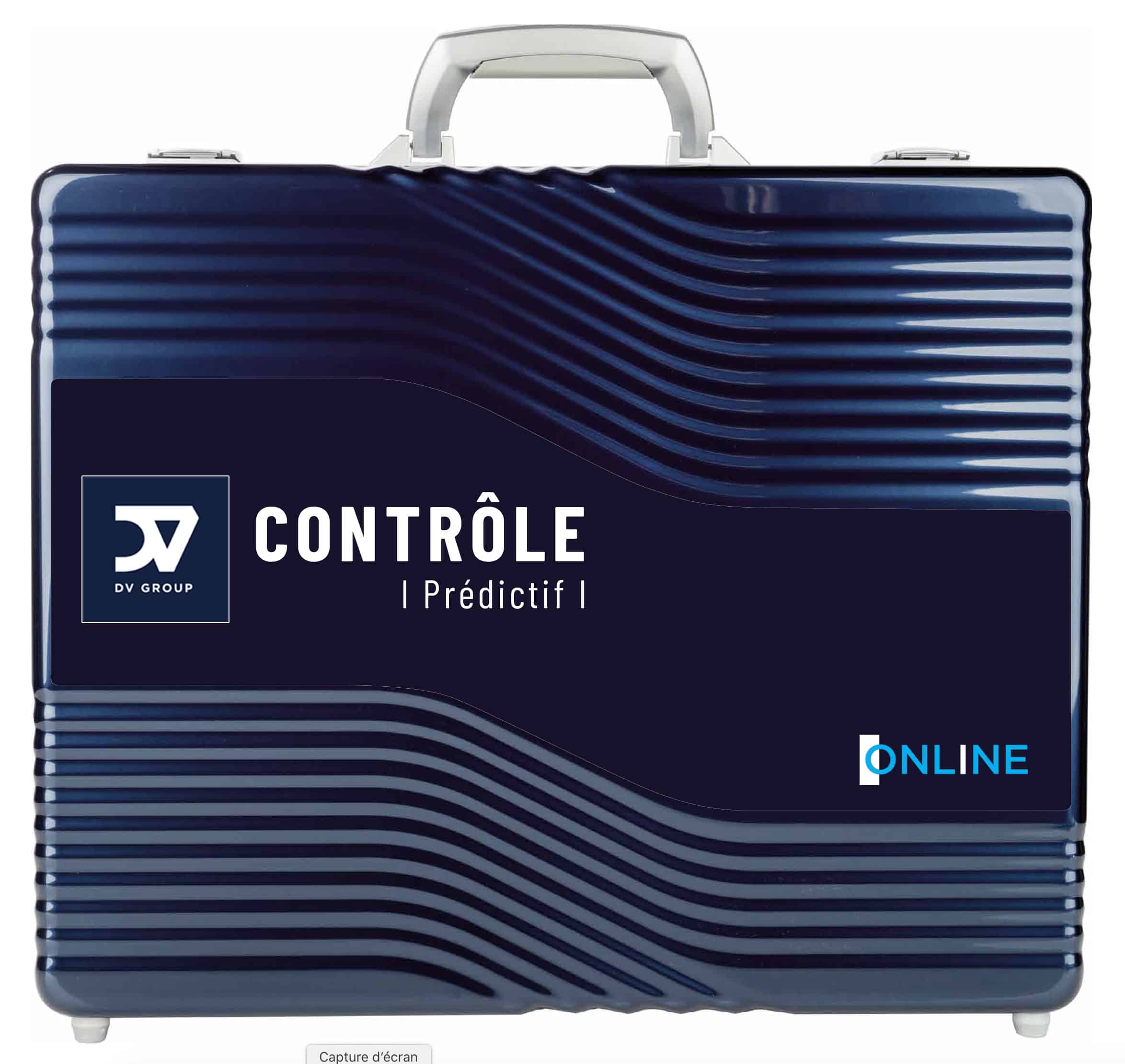
Gewinne und vorteile für den kunden
- Reduzierung der dreitägigen Wartungsarbeiten auf einen achtstündigen Arbeitsvorgang
- Vierfache Reduzierung der automatischen Schmierung
- Gehäusetemperatur des Trägers bei 40°C anstelle der ursprünglichen 70°C
- Reaktions- und Analysezeit im Falle einer sofortigen Abweichung
- Die an einem validierten Brecher getestete Lösung wird auf andere Anlagen in den Prozessabläufen des Kunden (Extruder, Belüftung usw.) übertragen.